Sennebogen material handlers meeting operational needs of European-based scrap recyclers
S. Norton, UK, and Zlompol Sp.J, Poland both finding success with latest Sennebogen purpose-built solutions
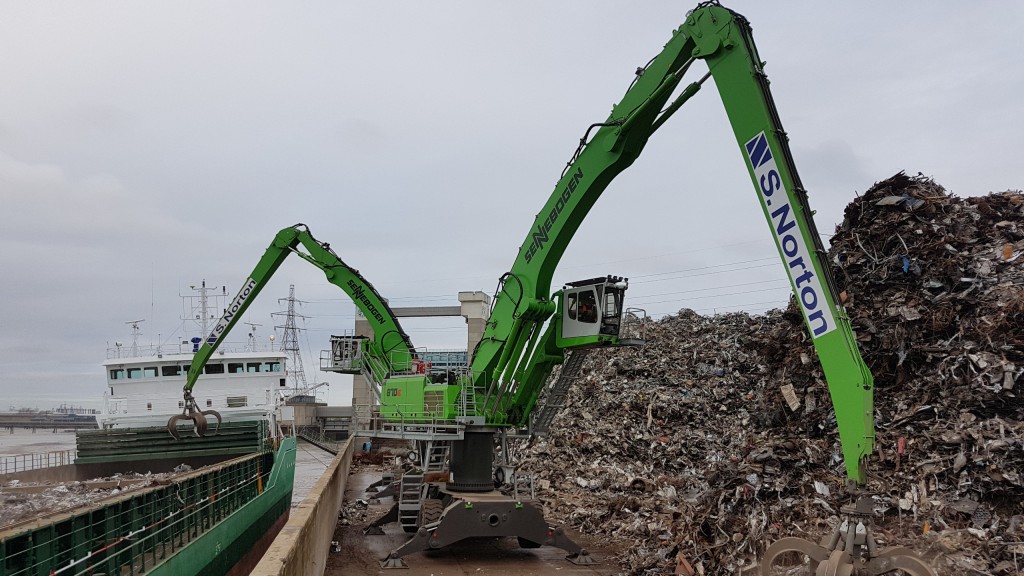
S. NORTON UPGRADES RIVER PORT CAPACITY GREEN HYBRID MATERIAL HANDLERS
Two new 206,30 lb. (93,500 kg), rubber-tired SENNEBOGEN 870 M material handlers are the centerpiece of a $14 million upgrade program at S. Norton & Co's ship-loading facility in Barking, UK.
Located on the Thames River, the Barking River Port serves vessels linking Greater London to the English Channel and the North Sea. The 870s are mounted on 6 ft. (1.8 m) pylons and fitted with a boom and stick giving it a 79 ft. (24 m) reach, larger outrigger pads for increased stability, and 3-yard 5-tine grabs. The machines also feature the Green Hybrid energy system, utilizing a large central boom cylinder to hydraulically capture "free" energy when the boom is lowered, then use the stored energy to assist each lift cycle.
Michael Duke, Site Manager for S. Norton's Barking facility, explained, "There have been SENNEBOGEN material handlers (835 Specials) on this site for over 12 years, and they have served us very well. The machines were getting up to 20,000 hours, so we knew we had to bring in replacement machines. As part of our overall development program, we needed to go for larger machines to increase throughput, by loading vessels much quicker."
Matt Norton, Technical Director, continued, "We visited SENNEBOGEN during the build process to inspect and test the machines before they were stripped down for shipping to the UK. The trucks arrived on the Monday, the machines were put together and handed over on Thursday evening the same week and it all ran like clockwork."
BALANCING FUTURE ENERGY COSTS AND EFFICIENCY in Poland
Zlompol Sp.J., based in Tarczyn in Poland is celebrating 25 years in the scrap recycling business with a new SENNEBOGEN 8100 EQ material handler. Managing Director Robert Cimoszynsk says the firm chose a machine that improves productivity while reducing energy costs and allows them to build their business at the same time.
"Our new machine can be seen from quite some distance away. People keep coming to admire it. Many people are even making special trips to bring scrap so they can see the new material handler."
The 8100's EQ counterbalance design which is a simple linkage continuously adjusts the machine's large counterweight to reduce the amount of energy required to lift each load. This allows a relatively small 110 kW electric motor to fully power the machine. Without the EQ advantage, a comparable hydraulic material handler would need at least a 200 kW motor to achieve equal power and operating area. Combining the balance principle and the electric drive saves the company up to 75% of the machine's operating costs. Working at an elevation of almost 35 ft. (10.7 m), the operator not only has an unobstructed view of the shredder feed area, but can also keep an eye on the entire yard and all the processes going on around him.