A new era of automation in recycling processing
The rise of technology is right on time to parry market pressure
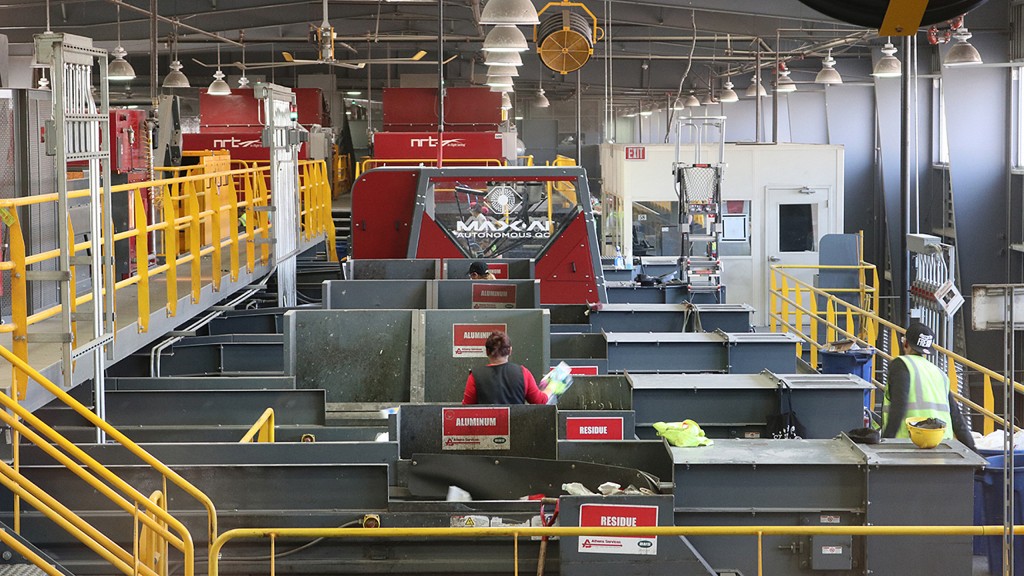
Industrial recycling at its core is a manufacturing process that creates products, but it is certainly not as simple or as streamlined as, for example, producing toothpicks. We don't have the luxury of controlled and predictable inputs, repeatable processes and identical outputs.
While other industries have been heavily automated for decades, recycling has remained dependent upon people controlling inputs, making decisions and directly participating in the production process through manual sorting. The largest hurdle to overcome remains the inherent nature of the waste stream; it's highly variable and unpredictable, and includes everything — including the kitchen sink.
The evolution of optical sorting
We've come a long way since the inception of materials recovery facilities (MRFs), making major advancements in technology and process design, including advanced optical sorting and the rise of the super MRF. Processing is more efficient and effective than it has ever been. But it's not good enough.
By now we're all familiar with China's National Sword policy and the impact it is having on our industry. The world's largest buyer of recycled commodities has demanded that we make them better. No longer is 87 octane sufficient, but 93 is demanded — and at the same price. Processors are spending more time and money to improve the purity of their products: slowing down their lines, hiring more sorters, and adding equipment.
These changes inherently mean increased capital expenditures and operational costs, and in many cases less production. While that may sound negative, the timing could not be better, because we're ready. Concurrent with the demand for increased quality comes new technology in the form of Artificial Intelligence (AI) that significantly disrupts the economics of our manufacturing process.
MAX-AI technology
People have historically played an important role in the industrial recycling process because of our ability to make sense of the variable and unpredictable nature of a waste stream. We use our eyes to see what's on a belt, our brains to think and make decisions and our hands to pick and place items in the proper chutes. Empowered by revolutionary, artificially intelligent (AI) technology, Max-AI from Bulk Handling Systems (BHS) now allows the Max-AI AQC (Autonomous Quality Control) robotic sorter to accomplish the same tasks that people can perform.
Fundamentally, Max-AI technology identifies recyclables in a similar way to a person. A process called deep learning runs through hundreds of thousands of images to train neural networks to "think out" the correct identification. Once built these neural networks resemble the architecture of the brain and, when paired with a camera, will correctly identify the items in our recycling stream in near-real time. Through training, Max is also able to very accurately identify items never seen before, based on probability. While this breakthrough technology seems complicated, we often find ourselves explaining it with the straightforward phrase: "If a person can identify where it belongs, so can Max."
Max-AI technology is changing the industry. In numerous plants around the world, the AQC is sorting containers at speeds faster than a manual sorter. There is no risk of Max being late, walking off the job or getting hurt. Perhaps the best part is that Max doesn't take breaks and can work multiple shifts. The Max-AI AQC is also at work on residue belts, pulling commodities that would otherwise go to landfill. Max-AI technology is also employed on paper sorting lines. BHS' recently announced RePower South project includes only four human sorters. As this technology matures, it will be common to have no sorters at all.
Economics and data in the MRF
Economics in the MRF change significantly without having to rely on 15, 20, 50 or more manual sorters. Consider the financial impact, when running two or three shifts is only marginally more expensive than running one. The labour savings alone account for millions of dollars every year the system is operational — not to mention the production benefits and savings from buying a smaller system that runs nearly all day. Suddenly, the addition of a few more optical sorters to increase purity looks much better on a pro forma basis. Rather than spending more and slowing down to produce less, subsequent generations of MRFs will automate more to boost production, purity and profits.
Additionally, Max-AI technology does more than empower robots to sort — it will provide recyclers with previously unavailable intelligence about their business. Could an operator look at a screen today and tell exactly what is in their PET bunker? With the Max-AI Visual Identification System (VIS), they can. VIS is Max-AI technology without the robot. VIS identifies material and collects data that are visualized through BHS' advanced controls and business intelligence software. It can alert an operator of material status or changes at any point in the system, and even certify a bale's contents.
Eventually, VIS will be used to dynamically optimize a system, making autonomous real-time adjustments to equipment including infeed, conveyors, screens, optical sorters, balers, and everything else. Even the best MRF operator couldn't possibly observe and comprehend what's on every conveyor, analyze it in real time, and make adjustments. Soon they won't have to try.
A new age of recycling automation
AI has enabled the recycling process to reach a new age of automation, where investments in new technology are a welcome addition in exchange for higher production, increased quality and much lower operational expenses. Again, the roadblock to fully automating our production process has been the nature of our waste streams being highly variable and unpredictable. This problem is solved with AI. This technology can now see, think and act. It's the beginning of a new era of automation, and it's going to be a fun ride.
This article was contributed by Bulk Handling Systems, and was originally published in the March, 2018 edition of Recycling Product News, volume 26, Number 2.