Richmond Steel Recycling: Auto Focus
The right processing equipment key to long-term success for Richmond Steel Recycling, B.C.’s only auto shredder
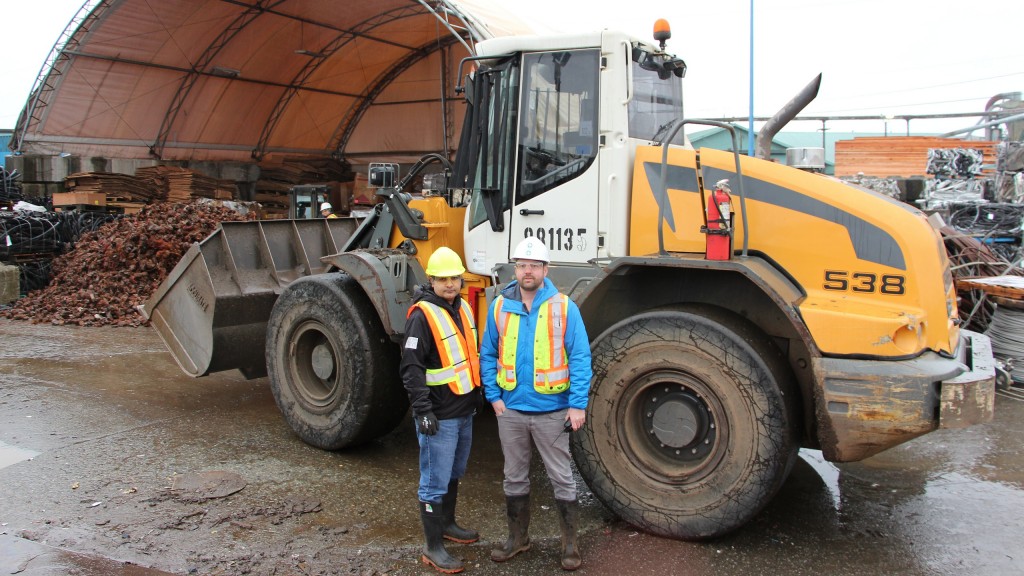
Richmond Steel Recycling has been in business for over 45 years, with operations starting in the early 1970s. Today Richmond Steel Recycling has four locations in B.C., with feeder yards in Prince George, Fort St. John and Kamloops. At their main yard, located on Mitchell Island, on the Fraser River between Richmond and Vancouver, B.C., they operate the province's only large-scale auto shredder.
Al Roadburg originally founded the business, in part as a response to the fact that in B.C. at the time, there was no place for end-of-life vehicles to be recycled. Scrap vehicles were largely ending up at landfills and piling up at the auto wreckers and "junkyards" of the day. In the mid 1970s the business was sold to a large corporation and the company has been through various corporate owners since. Since the 1990s, the company has been owned as a joint venture between Sims Metal Management and Nucor Corporation. The current general manager of Richmond Steel is Harbinder Dhillon who has been with the company for over 27 years.
"When Al Roadburg started Richmond Steel they installed a shredder and started recycling vehicles," explains John Rai, Richmond Steel Recycling's assistant manager and senior buyer. "The B.C. government helped recyclers at that time to go around the province crushing cars, and then they were transported to Richmond Steel. That was basically the genesis of the company."
Mitchell Island is a high-density industrial park surrounded by the north arm of the Fraser River. Rai says there has always been a lot of auto wreckers on the island and nearby, which is one of the reasons the shredder was originally installed there. The main reason for Richmond Steel's choice of location however, was the specific proximity to a steel mill which was also located on Mitchell Island at the time.
"Vancouver is very limited for industrial space," says Rai. "Over the years, many metal recyclers have opened up here on Mitchell Island. As the only shredder in B.C. currently, we work with recyclers from around Western Canada, Alaska and Washington State, as well as those located around Vancouver and right here on Mitchell Island with us."
Inflow and outflow
"We buy a lot of cars off auto wreckers," says John Rai. "Our main activity is shredding cars. So once auto wreckers are finished selling parts, de-polluted car bodies come to us. We've built very good relationships with B.C.'s auto wreckers and scrap recycling industry."
A portion of Richmond Steel's material supply comes directly from the company's three feeder yards in the B.C. interior and northern regions. The Prince George yard was opened up in about 1995, Fort St. John was added about 10 years later, and the Kamloops yard was acquired about five years ago.
"Any shreddable material the feeder yards get is shipped down to us via truck or rail," explains Rai. "Their cut grades of ferrous are prepared and shipped directly from their yard to Nucor Steel Seattle."
Outside of ELVs and other material collected and sent to their Mitchell Island yard from their three feeder locations, for end-of-life auto collection from scrap yards and auto wreckers, Richmond Steel Recycling uses OverBuilt mobile car crushers.
"When we first decided to replace our car crushers, we did our research," continues Rai. "OverBuilt had the features we wanted. These machines are very efficient in the way they process cars, provide excellent power for crushing, and quick cycles."
Rai adds that prior to buying their first OverBuilt machine, about 12 years ago, they used old crushers, dating from the 1970s and early 1980s, which had been welded, rebuilt and serviced for many years.
"We bought our first OverBuilt machine and were impressed with it," says Rai. "And then basically, within a couple years, we replaced our fleet. At one time, we had six of them. I think we're down to about four now. We're fans of our OverBuilt machines.
"The majority of our cars are collected from auto wreckers," he continues. "So they've already taken the parts they need, de-polluted the vehicles, removed the tires, etc. We do get a few ‘wet' end-of-life vehicles here, with fluids still in them. To facilitate that, we have a SEDA system to de-pollute the vehicles. We've been using the SEDA system for about five years and the guys like it."
For collection of ferrous materials from surrounding landfills, a Sierra International mobile baler is used.
Rai says Richmond Steel has been landfill baling for more than 35 years, since about the early 1980s. Using mobile balers, they pull metal out of the landfill and bale it for transport back to their yard.
"Our Sierra mobile balers go to landfills and will bale up materials, including a large amount of tin, for transport to our shredder, where we'll shred the bales," says Rai. "Typically, landfills are managed quite well these days. Most landfills have a metal pile. Some even call it a ‘baling pile.' When the trucks come in, they dump in separate piles. We basically just take care of the metal pile for them."
He adds that because landfills are generally remotely located, they'll typically put out tenders for collection of materials and companies will bid. "You need a mobile baler to really make this process worthwhile," he says. "You can't really ship light-gauge metal from landfills without a baler because the freight cost would be too much. You wouldn't be able to get enough weight on a truck."
Overall, Richmond Steel recycles thousands of tons of ELVs, white goods (household appliances) and other material on a monthly basis, and also processes a great deal of nonferrous material. Using a Harris Baler at their main yard, baled nonferrous material is sold to global markets.
For ferrous materials, because Richmond Steel is owned by Sims and Nucor, both of which are global corporations involved heavily in steel recycling and manufacturing, they have the benefit of operating with a set buyer. Ferrous end product, bulk shred produced by their shredder, is sold domestically to Nucor Steel's mill in Seattle, Washington.
Process and equipment
Richmond Steel's ferrous shredder, also known as an auto shredder, was supplied by Metso Texas Shredder, but consists of various components, and is powered by a 4,000 horsepower ATB Schorch electric motor.
"The shredder, by its nature, dictates what it can shred," explains Rai. "So the process mainly dictates lighter gauge metal, including the lighter gauge metals found in automobiles and household metal appliances."
In 2012, their shredder was largely replaced. Brett Matheson, one of Richmond Steel's commercial buyers, says "At that point, its capacity to shred various grades, such as HMS 2 improved." (HMS 2 is Heavy Metal Steel - steel and wrought iron containing galvanized and blackened steel.)
"When material arrives here, the first part of the shredding process begins at our entry," continues Matheson. "Everything is run through a radiation detector. So nothing can go to the shredder that hasn't gone through the detector."
Once incoming material is weighed, scanned and recorded, then it moves into the yard. "If it's shreddable material, it's directed towards the shredder intake area," explains Rai. "At that point, if it's in a self-dumper, the truck will dump. If it needs to be unloaded, for example, like with a load of cars on a flat deck, we use scrap handlers to unload. These same scrap handlers feed the shredders via infeed conveyor. All of our scrap handlers are Liebherr machines."
He says there's usually two scrap handlers at the shredder on a normal busy day - one helping to unload, and one feeding the shredder and helping to unload in between feeding the shredder.
"In the Richmond yard, we have three Liebherr handlers," says Rai. "We've been running Liebherr since about the mid-1990s, and just Liebherrs. We like them."
Rai explains that cutting of large ferrous materials is done in one of two ways. "We have ‘burners' (employees who torch cut) and we use a mobile shear mounted on a Cat excavator."
For end-of-life autos, if it has not been done at source, vehicles have their tires removed, fluids removed, batteries removed and mercury switches removed.
"The rest of the car is put through the shredder which separates the metal from the foam and the seats and the carpet and plastics," explains Rai.
"We separate loads of iron and aluminum, and also buy transmissions, aluminum engine blocks and any other form of iron and aluminum," Matheson adds.
"Beside our shredder, we have a separate process called the metals recovery plant. That's where shredded materials are separated into nonferrous grains."
According to Rai and Matheson, the nonferrous side of their operation is a very key component, but one which differs greatly from the ferrous business.
"We've got a Harris nonferrous baler," says Rai. "Whereas we have to shred steel and separate its components, usually nonferrous is separated and baled as opposed to being shredded. Copper and aluminum and wires, including insulated wires, are separated and baled.
"We'll also shred aluminum or other materials," he continues. "When we get material in that can't be sold as nonferrous in the state that it's in, it will go through the shredder, and then through the MRP (metals recovery plant).
"Sometimes, material is just way too big to be baled. A good example of what we call ‘ferrous other' would be a reefer trailer. It may have aluminum flooring and aluminum skin. But the frame will be steel and the chassis that it's sitting on, and axles will be steel. And it could contain foam insulation that needs to be separated. Something like that would be shredded, and then the material separated."
Success in a changing industry
John Rai says he's noticed several elements of the industry that have changed significantly over the last decade or so. He says one thing that has happened is that the "playing field" has been levelled to a certain extent.
"In the last ten years, I would say the big change is that everyone is starting to come to a level playing field, with a uniformity and a more professional way in which business is done," comments Rai. He says this has much to do with the various environmental regulations that have been put in place and notes that the auto wrecker (or auto salvage) sector has updated their environmental regulations and associations over the last decade as well. "I think that's made everybody put more structure to the process of auto recovery, so that everyone is competing at the same level," he says.
When it comes to metal theft, because Richmond Steel's incoming supply is mostly from commercial sources and their own feeder yards, they don't have to deal with the issue as much as many of the smaller scrap yards would, where there is more supply coming from the general public.
"Of course, if anyone from the general public comes to our yard, we scan their driver's license and comply with all regulations," adds Matheson. "But generally, this is a small portion of our business. Most of our business is with dealers and from large industrial accounts."
When asked about the current situation with respect to tightened import restrictions for recyclable materials in the Chinese market, Matheson says, "Currently, everyone's talking about China, but they've basically been building up to this for several years, receiving specs and quality controls and changing the way business is done.
"China started a CCIC inspection program ten or twelve years ago," he continues. "Now they have the National Sword. Limits have been put on transactions, and while environmental regulations have been there for many years, I see more companies meeting them, big or small."
For Richmond Steel, because their main buyer for ferrous is set, domestically, with Nucor Steel Seattle, the current Chinese restrictions have not affected this side of their business much at all.
But nonferrous still relies on end-markets overseas, or domestically, wherever the market is the strongest on a given day. So with the recent import restrictions coming out of China, Matheson says it has affected their nonferrous program somewhat.
"It's made it more difficult to sell certain items to lower recovery, like wires, motors, alternators and product such as that," he says. "The clean material hasn't been much of an issue. But at the end of 2017, a lot of the quotas were running out overseas. So, we find it a little more difficult to sell into certain markets."
He says this means they will both look to find markets outside of China, and work to increase the purity of the material being produced.
"Right now, we're cleaning up our shredded aluminum, our Zorba, differently because it's got to be cleaner than it has been in the past," says Matheson. "Either new markets will emerge, or new technology will come out to enable us to produce a cleaner product." RPN
This article was originally published in the March 2018 edition of Recycling Product News, Volume 26, Number 2.