Shredding and grinding solution boosts plastic waste handling capacity for Midwest recycler
Lindner's tailor-made re-grinding line has increased output and growth for Winco Plastics
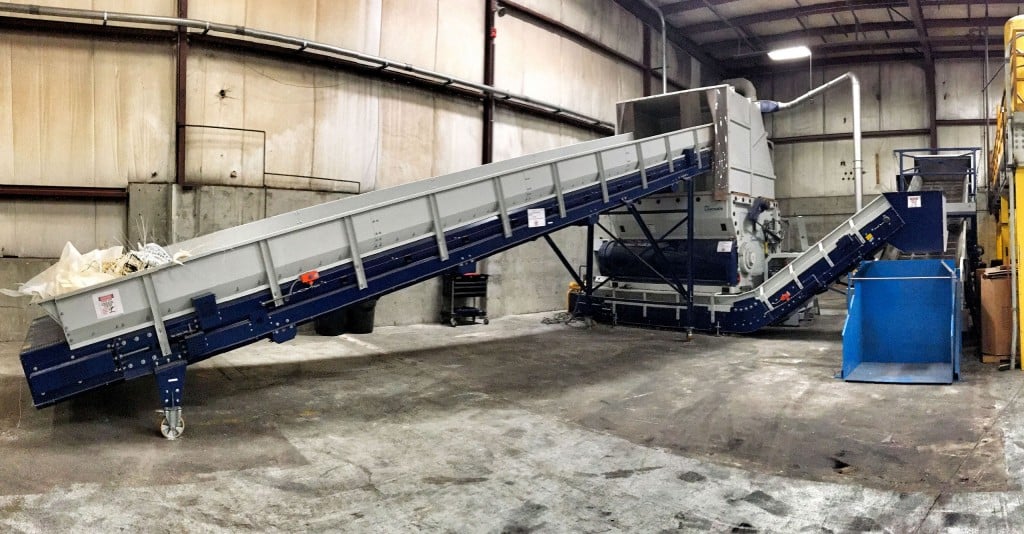
Winco Plastics, North Aurora, IL., USA, a subdivision of Winco Trading (www.wincotrading.com), is one of the largest full service plastic recycling companies in the Midwest with 30 years' experience. After purchasing a Lindner re-grinding line including a Micromat Plus 2500 pre-shredding system and an LG 1500-800 grinder, Winco have significantly increased their plastics waste handling capacity, making them one of the fastest growing companies in their sector in 2016. The range of rigid materials fed into their Lindner system includes HDPE pipes of any size and thickness, HDPE sheets, PE and PP purge, and PC sheet as well as PET, mainly from post-industrial sources such as automotive and others.
Tim Martin, President of Winco Plastics, confirms an output of 4,000 to 6,000 lbs. of 1/2" regrind material per hour, ready for sale to the company's clients for further processing in the recycling loop. "One major reason for our decision to purchase Lindner's re-grinding line was its ability to handle the wide variety of size, weight and form of the expected input material coming from different suppliers", he says. "We were happy to see that Lindner's re-grind line is designed to shred heavy parts including pipes up to 8' long, purges and logs up to Gaylord size as well as light material which can be directly ground without a pre-shredding process. What convinced us even more was that all of this is backed by a high level of sustainability, particularly low power consumption, as well as low-maintenance operation with virtually no rotor wear and a maintenance-friendly layout thanks to the specially designed maintenance flap, which makes cleaning and maintenance very easy and convenient without requiring staff to climb inside the hopper. We believed that at the end of the day this combination of plus points would pave the way to a highly cost efficient recycling process."
Lindner Recyclingtech America LLC, the US branch of Austrian company Lindner Recyclingtech, offered Winco a tailor-made re-grinding line which exactly met their specific needs. In a first step the delivered plastic waste is transferred to a heavy duty feeding belt conveyor, designed to handle all kinds of material loaded by forklift or Gaylord dumper, followed by a 180 HP Micromat Plus 2500. This high performance single-shaft shredder is equipped with a customized (higher) internal ram enabling high throughput of all input materials as well as a new overlapping rotor (length 98") to avoid bridging of material between ram and rotor during the shredding process. The rotor carries fourfold reversible 1.69" x 1.69" Monofix knives which further assist high productivity operation whilst at the same time facilitating cutting blade replacement and maintenance.
The pre-shredded material is discharged from the Micromat by two successive belt conveyors, one of them equipped with a Gaylord dumper for handling any scrap suitable for direct feed into the downstream 175 HP LG 1500-800 grinder without prior pre-shredding. This universal heavy duty Lindner grinder is equipped with a large feed opening (61 1/2″ x 31 1/2″) and a 98" long rotor with a diameter of 25", carrying 7 knives and 2 counter knives, making it a first choice for recovering heavy and bulky rigid scrap as well as for second step grinding of pre-shredded material with high output rates.
As Tomas Kepka, Sales Director Plastic Division - Lindner Recyclingtech America LLC, recalls: "An initial challenge was to provide a system which would completely fit into the customer's limited shredding area. Thanks to compact design of Lindner's systems, the complete regrind line could be installed on just 1200 sq. feet, leaving plenty of space for operation and maintenance." And he also highlights the uncompromisingly safe and secure operation of the system in spite of the partly undefined input material. "Being basically very sensitive to any contamination, the Lindner system is equipped with dual protection technology including a safety clutch on the Micromat 2500 shredder and a metal detector installed on the feeding conveyor into the LG 1500-800 grinder. In addition, the rotor is protected by a highly effective hard coat to extend lifetime when shredding abrasive material."
And Martin sums up: "We chose Lindner for our shredding line because of their engineering knowledge and long experience in the plastics recycling industry. They had several references worldwide showing them to be a reliable partner for customized shredding projects. Their systems are heavy duty, which is an absolute necessity for our daily operations. Lindner's experienced project team was very helpful from day one and they were able to supply a full shredding line including complete control, installation and electrical work to ensure the line would be operational in a timely manner. With hindsight, our decision to accept Lindner's offer was absolutely correct. The complete system went into operation in March 2016 after a lead time of only 4 months. Its energy consumption is even lower than expected and its performance is outstanding!"
Winco Plastics, North Aurora, IL/USA, is a full service plastics recycling company which not only offers toll grinding, but also buys, sells and processes plastics resin, including contaminated waste, floor sweeps, powder, pellets, and plastics recycling materials including engineering and commodity. Over the number of years that Winco Plastics has been in business, the company has earned an outstanding reputation due to its focus on sharing knowledge and handling of the various types of plastics. This has resulted in the development of long term relationships with its clients.
Lindner Recyclingtech America LLC, Statesville NC, is the North American subsidiary of the Spittal, Austria based Lindner-Group (www.l-rt.com) which has for decades been offering innovative and successful shredding solutions. From the original planning, development and design to the production and after-sales service, everything is supplied from a single source. At its Austrian production sites in Spittal an der Drau and Feistritz an der Drau, Lindner manufactures machines and plant components that are exported to nearly one hundred countries around the world. Beyond stationary and mobile crushing and shredding machines for waste recycling, its portfolio includes complete systems for plastics recycling and the processing of substitute fuels and substrates for biomass equipment. A team of sales and service experts located throughout the United States provides support to clients in the USA and Canada.