Advancing the sort with robotics
Carton Council pilot project at Colorado MRF using artificial intelligence to improve separation
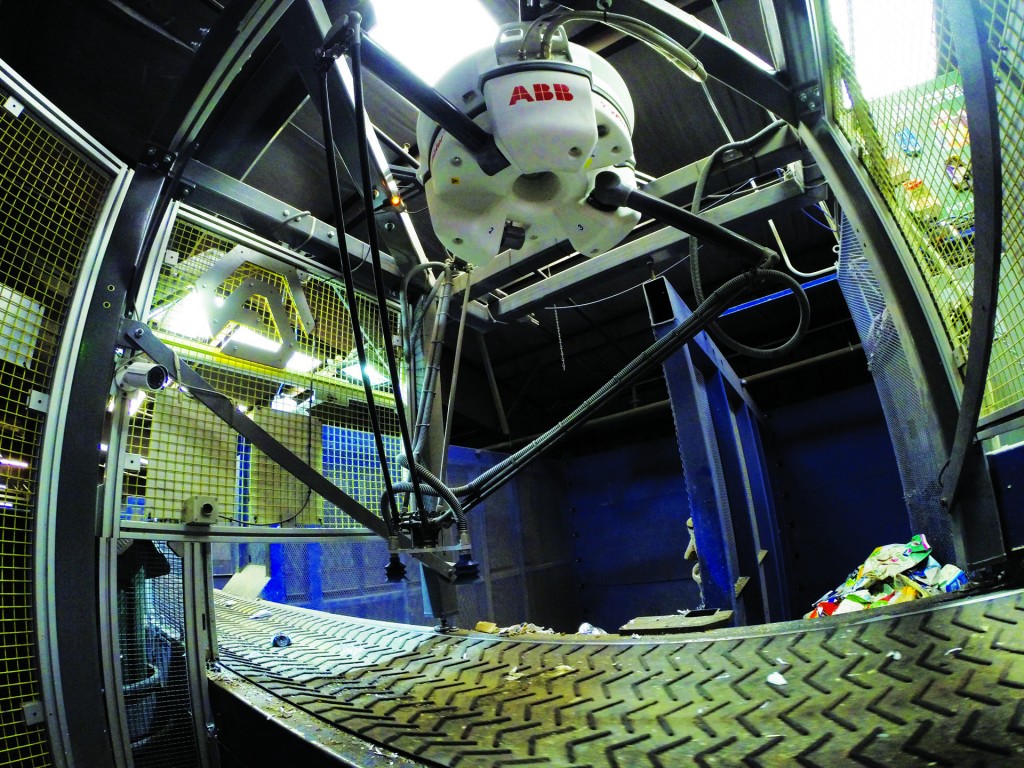
Sorting of food and beverage cartons is a challenge for most MRFs in the recycling industry. It's a tough job that is today mostly done by human pickers who need to move fast and quickly recognize the products going past on the line before separating them from the overall waste stream.
Because of the combined nature of the material, it has been difficult to apply technology to sorting lines in most sectors of recycling. However, improvements in machine learning and artificial intelligence have led to a pilot project using cutting-edge robotics to improve the return from sorting tables.
Alpine Waste & Recycling, based in Denver, Colorado, has partnered with AMP Robotics and the Carton Council of North America to test a robotic system designed to identify the wide variety of food and beverage cartons passing by on the sorting line, and to separate them from the stream.
The flow of material in recycling makes good sense for robotics, but the complexity has kept higher levels of sorting technology out of the industry thus far, explained AMP founder Matanya Horowitz.
"We saw an opportunity to use a lot of robotics technology that has been common in manufacturing, agriculture and other areas for quite some time," Horowitz said. "We saw that this machinery hasn't made it into the recycling industry because of some technical challenges - namely, you have a tremendous variety of different materials, whether it's carton, different kinds of newspaper or plastics, and there's no consistency. All that material is folded and dirty and crunched together in different ways. It's very challenging to teach robots or other forms of machinery where one carton ends and a plastic bottle begins."
Despite those challenges, Horowitz said there was still a great opportunity to develop a new approach to sorting. That hinged on taking advantage of the growing field of machine learning - helping computerized systems educate themselves on the job.
The Pilot at Alpine Waste & Recycling
Thanks to a grant from the Carton Council, AMP developed the Cortex, a robotic unit with specialized grippers on long spider-like "arms" that allow it to pick up material from moving belts. Constructing the robot - nicknamed "Clarke" after the science-fiction author and futurist Arthur C. Clarke - was the easy part. Educating it was another thing entirely.
"This technology goes after all the different categories of material, the different plastics, cartons and fibre products," Horowitz said. "Rather than program in the material that we'd like the robots to be able to separate, we have a set of algorithms based on machine learning that let it actually learn from experience. So, what we do is show it thousands of examples of bottles, cans and cartons, and it begins to learn what distinguishes all of them."
Using an optical scanning system, Clarke can begin to distinguish items based on various characteristics; a soda company logo, for example, would likely be found on number one plastics, and the robot will then treat the item bearing that logo in that manner, learning with each piece of material it handles.
"The result is that it uses much the same information as you or I might use if we were separating out these things by hand. Pretty much anything that a person can visually distinguish, the robot can distinguish," Horowitz explained. "But, while the robot may be only separating out cartons in one use, the vision system still sees all the material, gathers that information and learns from the entire waste stream."
Alpine and AMP started their pilot project in early 2016. Clarke is the result of extensive testing and was installed in December after numerous details were ironed out surrounding such issues as reducing dust problems - challenging in any MRF - and how best to pick out cartons from the waste stream.
"There were a lot of little details that you need to get right before you have a system that is actually useful within that challenging work environment," Horowitz said.
The results so far have been encouraging, he noted, most notably in the speed that the robot can deal with passing material.
"We're excited about getting to 60 picks per minute - that makes it so that the space the robot occupies is comparable or above the status quo for existing sorters," Horowitz said. "We wanted to make sure that if you're going to put in a robot that your capacity is only going to get better."
Labour and productivity benefits
The system has proven to be solid in terms of uptime, with the capability to run long shifts with minimal maintenance and supervision, which means benefits to the MRF in terms of guaranteeing a steady flow of saleable material.
"The robot is becoming a very reliable piece of machinery, and the result of that is that facilities can count on it to show up every day for work. Many facilities have different challenges when it comes to sourcing enough people to actually work the sorting line," Horowitz noted. "This opens up different opportunities for them to redeploy existing personnel to recover other valuable material."
In addition, as the technology improves, robots like Clarke can start sorting more than one material from a line - and if multiple systems are installed, that means a significant improvement in recovery.
"On a sort line that might be 15 feet long, depending on the throughput needs you have, you might actually have several robots... they fit very nicely into existing MRFs," Horowitz said. "We require almost no change to the existing operations, so we think there's going to be a lot of appeal in these for MRFs in the future. They can basically achieve carton automation, or automation for other materials, with very little upfront hassle."
While the initial thrust of the project was to increase return on cartons, that potential to expand into other valuable products is a big part of the benefits, according to the Carton Council.
"Clarke greatly expands opportunities for the carton industry as we work to increase the efficiency of carton recycling and, ultimately, divert more cartons from landfills," said Jason Pelz, vice president of recycling projects for the Carton Council of North America and vice president, environment for Tetra Pack cluster Americas. "Everything Clarke has learned about identifying cartons can be transferred to robots at other MRFs. We are excited to bring innovation to carton recycling and believe this technology has widespread implications for the recycling industry, as it can be adapted to other materials."
The value proposition of the AMP Cortex system will be attractive to MRF operators in the long term as well, Horowitz said.
"Payback time can depend a great deal on the number of shifts and other details such as throughput compared to the existing operations, but we can offer roughly less than a three-year payback, and typically less than that," he said.
In addition, AMP is offering two models - one is the direct sale approach, where the facility buys the unit outright, and the other is an operating lease through which the facility would pay a monthly fee to keep the robot operating.
"In that case, the payback period can be very, very good and they don't have to worry about the robot too much," Horowitz pointed out. "We provide a warranty, we provide continuous software updates, and the path to automation has very few hurdles at that point. Combined with the low footprint of these systems, we think we'll be opening up the capacity for more diversion within a wide number of recycling facilities."
This article was originally published in Recycling Product News, April 2017, Volume 25, Number 3.