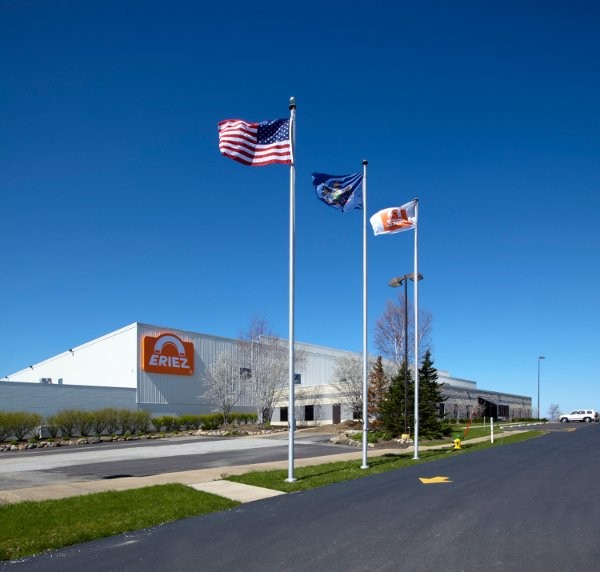
Omaha, Nebraska-based Firstar Fiber Corporation is one of the region’s largest full-service recycling companies. In 2006, Firstar launched the state’s only material recovery facility to process single stream commingled recyclables for both residential and commercial customers. The company also began a program called “Curbside Rewards!”, which has successfully enabled households in Nebraska and Iowa to receive rewards for participating in recycling.
Firstar has expanded beyond its local roots by marketing to some of the largest and most respected regional, national and international end markets for a wide range of paper, plastics and other recyclables, thanks to a major renovation in 2008. Included in the overhaul was the installation of the company’s first Eddy Current Separator (ECS) manufactured by Eriez.
According to Maintenance Supervisor Irv Wattier, Firstar has relied on their new ECS to effectively remove aluminum used beverage cans (UBCs) from its MRF recyclable products. Through the induction of eddy currents and the resulting repelling forces, the magnetic field repels the nonferrous aluminum and physically separates it from the plastic, glass, paper, etc.
“We used to sort the aluminum by hand, but now we run the aluminum UBCs and commingled recyclables over the ECS. We pull coloured bottles off the line before the rest is sent through the ECS,” Wattier says.
Relying on service
With the volume of commingled recyclables conveyed through Firstar’s ECS machine and around-the-clock use, over time, the unit’s rotor needed to be refurbished and placed back on-line with minimal downtime.
“In these cases, Eriez would send a 5-Star Service technician to our facility to handle the refurbishing work,” says Wattier. “Their service is consistently fast and effective.”
In January 2010, Firstar decided to switch out the older version ECS rotor to a newer Eriez off-shaft rotor design. At that point, Wattier also relied on the company’s consultation regarding the proper way to install the new, cutting-edge rotor.
“With the guidance and assistance from the Eriez- 5-Star Service team, our maintenance staff was able to easily install the rotor onsite with minimal downtime,” Wattier recalls. “The job was not out of our ability. With the help of the 5-Star team, we accomplished it.”
“The 5-Star Service group sent drawings for the new rotor installation and told us how to make the required adapter plates and spacers,” says Wattier. “The housing for the new design bearing is higher up on the ECS, so we had to raise the back end of the drag pulley and put in spacers to make it level. The 5-Star team walked us through that process,” Wattier recounts.
“Our team is ready to do whatever it takes to address customers’ issues and limit costly downtime,” states Jim Lasko, Eriez 5-Star Service Center Manager. “We use original OEM parts, remanufacture equipment to original specifications and offer ‘as new’ warranties.”
Eriez 5-Star service centre, located in Erie, Pennsylvania, employs trained technicians and has all the machining, fabricating and welding capabilities necessary to rebuild equipment quickly and accurately. Lasko says their service includes regular equipment checks, in-plant certifications and detailed reports, all to help customers minimize equipment problems and achieve maximum productivity.
“Checking equipment on a routine basis can identify problems before they become costly issues involving broken equipment and lost production time,” says Lasko. With the design work and subsequent consultation from 5-Star Service, Firstar’s new off-shaft design rotor is performing as promised, according to Wattier.
“The change to the new rotor is as different as night and day,” he says. “Other than bi-weekly greasing, this is a totally no-maintenance system. Everything is going great; we even purchased a second rotor to serve as a back-up. That’s pretty important because the ECS runs 24 hours a day, Monday morning through Saturday morning.”
According to Wattier, the maintenance on their newer off-shaft design rotor is also made easier since the bearing system is outside the rotor, where the bearings are more accessible to lubing and general care.
“It requires less maintenance now that the bearings are not tucked up inside the rotor,” he says. “When we received the new bearing, everything was ready to go,” Wattier remembers. “We chose to install the new rotor on-site rather than shipping the ECS out so we could avoid some downtime.”
“With assistance from Eriez’ 5-Star Service Group, we got up and running within two days.”