After the fort McMurray fire: Taking on demolition and debris recovery
Alberta’s Concrete Army is finding their legs in demolition and recyclables recovery in a big way, with help from Terrafirma specialty equipment
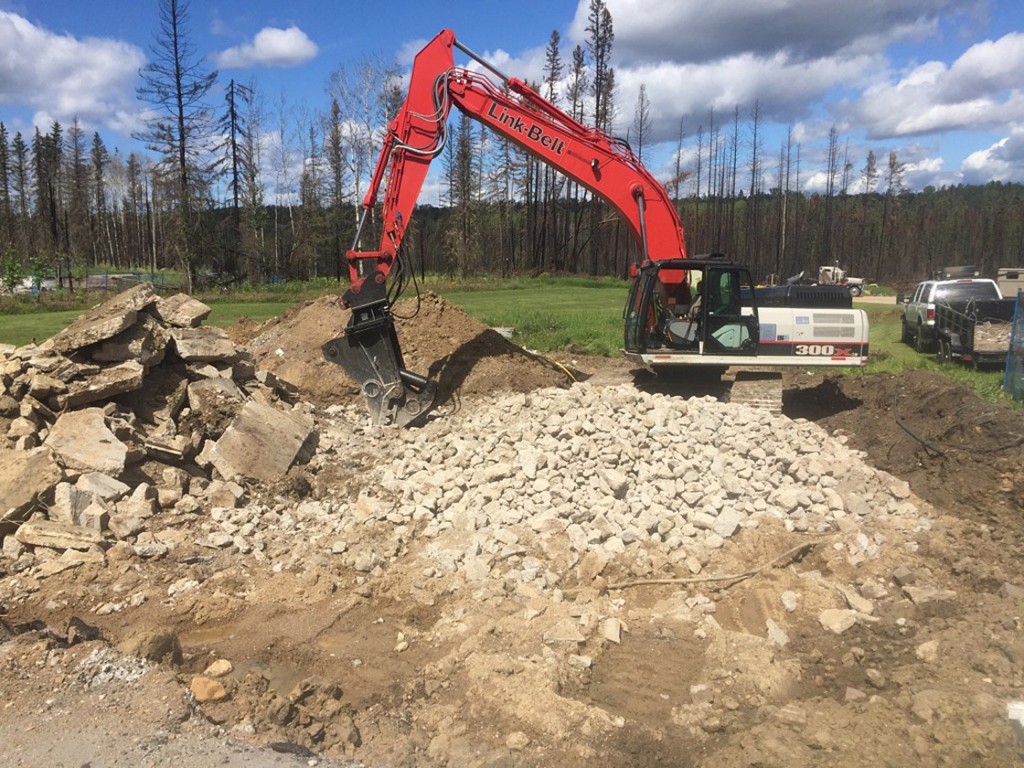
The 2016 Horse River Fire, which ravaged the Wood Buffalo Region of Northern Alberta and Saskatchewan, and which burned through the city of Fort McMurray, Alberta, destroyed close to 600,000 hectares by the time it was over. On May 1, 2016, the wildfire began southwest of Fort McMurray. On May 3 it swept through the community, destroying approximately 2,400 homes and businesses, and forced the largest wildfire evacuation in Albertan history.
Kevin Macdonald is the owner of 123 Developments Inc. based out of Fort McMurray. He’s been operating the company since the late 90s and has focused mainly on his specialty in concrete formwork. His company is also known in the region as the Concrete Army. In 2011, the company got into material handling, hauling all types of aggregate to sites around Fort McMurray. A more recent growth area for Macdonald, is demolition and materials recovery.
“By the time the cleanup in Fort McMurray is done, we’re going to be turning over somewhere between 50 and 200 houses,” says Macdonald. “This will include both old salvage, concrete salvage and all the debris removal on top of that. We have rented a range of specialty equipment from local equipment supplier, TerraFirma Equipment, which is getting us a good deal of specific business.”
Macdonald’s equipment from TerraFirma includes a Link-Belt 160 excavator and a Cat 336 EL excavator, both tracked machines, along with a Bateman BHM9-40 GA HydraMag, an Atlas Copco MG1000 Multi-Grapple and a Cat Vibra-Ram P25 pulverizer, and cleaning and digging buckets.
“On the big apartment complexes and underground parkades that burnt down, that’s where we’ll be brought in to do a lot of the demolition work. And then re-excavation for foundations, of course, we’re following the cleanup with foundation work for new homes and buildings.”
After the fire, concrete made up most of what was left. Temperatures during the fire were around 3,500 degrees. According to Macdonald, from a full structure, or the average house with a garage attached, he is taking away anywhere from one to three tandem gravel truck loads of debris, over and above the steel and the concrete that are removed from each site.
“For recycled concrete that we’re hauling out, we try to find businesses or homeowners that are going to have an immediate use for the product. We know a lot of people that own land in the area. So, we’ll provide the recovered concrete to them. We’ve been using a Cat [Vibra-Ram P25] pulverizing head, mounted on a Cat 336 EL excavator, as well as our Link-Belt 160 excavator.” Both carriers, he says, are tracked machines, selected for low ground pressure.
“We’ll take concrete down to about a 12-inch minus and bring it to the buyer. The contaminants, metal and other debris are completely removed so it can run through a crusher, and they can use it to put a sub-base down, as a cap for their yards or their warehouses to be built on, and for projects such as parking lot upgrades.”
On a typical job, Macdonald demolishes material and then runs it through a bucket crusher, which produces a stockpile of recovered material that can be sold as sub-base. To transport crushed concrete to local buyers he runs a fleet of 25 trucks, including live-bottom trailers, end-dumps and tandems. Local recycler, Sunset Salvage, located nearby, has been their destination for a significant amount of steel and other recyclables and debris they have removed.
With respect to recovered steel, Macdonald says some destroyed houses have produced anywhere from half an end-dump load to two. (One end-dump volume being approximately 28 to 29 yards of un-compacted material.) All of the steel pulled out by the Concrete Army is being hauled to Sunset Recycling. Macdonald says that back in June there were many abandoned refrigerators and other appliances lining the streets in some places, but those have since been recovered.
Working the demolition and recovery
The first thing Macdonald and his Concrete Army do upon arriving to one of the burned sites in Fort McMurray where demolition has been authorized to occur, is go over some of the site specifics. Typically it has been taking about two days to complete a demolition and site cleanup.
“First off, you want to make sure that sites are free of any hazardous materials, such as gun shells, rifle shells, propane tanks, chemicals, gardening and kitchen chemicals. Most of it would have been burnt up. But you’ve got to go through the process, make sure that all the hazardous materials are controlled. Once the project gets going, first we need to locate, expose, cut and cap any of the water, power, phone and gas lines on the property. The correct contractors are brought in to terminate any lines, and trenches are back-filled. The next step is sweeping the entire site.
“TerraFirma’s supplied us with power magnets [the BHM9-40 GA Hydramag from Bateman Manufacturing]. We’ll sweep the site and collect all the steel. The power magnet is a big circular magnet. You grab it from the top, it’s got a clamp-head on it. And then you hang it, hook it up, and it’s got its own hydraulic motor. We sweep the site with our power magnet, and throw all the metal into our end-dumps or into supply bins.”
Once the steel is off-site, Macdonald’s Concrete Army scrapes down the exterior of the site from the back end as far as they can reach forward. Material is placed aside and they move up to the front of the site and switch to their power grapple, [an Atlas Copco MG 1000 Multi-Grapple], for the debris cleanup.
“One of the benefits of using our power grapple is that it creates little dust or disturbance to the ground,” says Macdonald. “The OH&S folks are concerned about dust control and airborne contamination. With the power grapple, instead of just picking up material like you would with a bucket, where you’re missing a lot of the material in your scooping process and having to drag it a long ways, there is very low disturbance. You can come right over top of the material, just squeeze onto it and pick it up. It also lets us get right to the bottom of material and get it very clean on the concrete floor base, gives us the ability to pick corner-to-corner without having to do any shovel work, and allows us to rotate material and pick through it in different areas.
“Once we finish removing all the ash debris with our power grapple and Link-Belt, we’ll switch out and we’ll bring in the Cat 336 excavator. We’ll just put the big bucket on the machine with a thumb to start with. We’ll knock down a lot of the concrete, and pull up a lot of the slabs with the teeth. And then we’ll switch to our pulverizing head, and we’ll start pulverizing the walls and slabs – all the concrete. We reduce it down so that we can pull the rebar and all the steel out of it. The steel will get thrown to one side, the concrete to the other. And once we get it all separated and all the concrete reduced to a 12-inch minus, then the steel is picked separately. Then we’ll bring the 160 back in and use the power grapple to finish loading the pulverized concrete.”
Any leftover steel at this point is transported for recycling and concrete goes into end-dumps for transport to buyers.
“A big difference for us has been our Link-Belt 160 with the power magnet and the grapple,” says Macdonald. “You could complete the whole job with just the 160 Link-Belt and those attachments. But the pulverizing head on the Cat allows us to reduce the material to a clean, 12-inch minus. A lot of guys are taking a larger-sized slab, but this is a lot harder on the end-dump equipment. It’s our equipment, we want to take care of it. Secondly, with larger slabs you’re providing material that you’re not supposed to, which contains embedded rebar. Material is supposed to be contaminant-free, which means steel-free.”
According to Macdonald, the equipment they’ve rented from TerraFirma is providing a huge advantage over the competition, enabling them to provide a higher quality job, and to handle materials in a way that doesn’t damage the sub-base that the new foundations have to sit on, which is extremely important.
“It is good to be able to recycle material, considered to be waste by many insurance companies and homeowners, into sub-base for parking lots and other construction, and use it for foundation material for new homes, all of which is worth millions of dollars. Especially here in Fort McMurray, where we have a dwindling supply of aggregates. Recycled concrete offers an excellent sub-base material. It’s got all the qualities that you’d be looking for in a good 75-ml road crush. And demolished concrete product makes up about 95 percent of the recyclable material that we have to deal with.
“For us, with the help of TerraFirma Equipment and the specialized equipment they recommend and make available to us, the demolition and materials recovery side of our business is proving to be very interesting. It’s not entirely new, but new on a larger scale, and I’d like to continue to take it large scale here in Fort McMurray. So far, it has been a big boost for us to be able to do a lot more of it.”
This article originally appeared in the September, 2016 edition of Recycling Product News, Volume 24, Number 6.