Profitable and practical plastics reuse and recycling for the circular economy
Pilots in healthcare and the industrial sector demonstrating how it's done
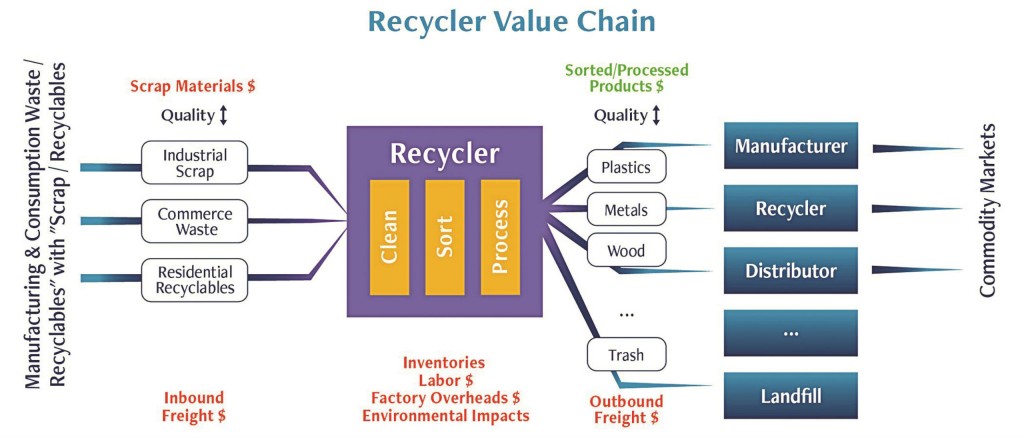
Profitable and responsible reuse and recycling of plastics from products, packaging and scrap is an enormous business opportunity – especially given today’s economic and environmental waste of most plastics. Realizing this opportunity requires a keen understanding of markets, material, equipment, input-output data and environmental metrics, as well as effective collaboration among multiple stakeholders in the plastics value chain.
With the currently low price of petroleum reducing the cost of virgin plastics, a successful plastics reuse and recycling business needs to carefully balance material- dependent processing costs with what the market will bear. Pilots in the healthcare and industrial sectors are currently being conducted to discover the most practical, profitable and responsible ways of doing so. All industries can learn from these two examples.
Healthcare sector pilot for plastics recycling
Globally, only 14 percent of plastic packaging is collected for recycling. According to the 2016 report, “The New Plastics Economy: Rethinking the Future of Plastics”, after losses from sorting and reprocessing, “only five percent of material value is retained for a subsequent use.” This report found that projecting from current levels of production of 311 million tons of plastics, to a doubling over the next 20 years, the plastics sector is expected to account for 20 percent of total oil consumption and 15 percent of the global annual carbon budget. Recovering value from post-first-use plastics therefore represents a monumental environmental opportunity.
Hospitals generate 33.8 pounds of waste per staffed bed per day, of which 85 percent is free from patient contact and infectious contamination. The Healthcare Plastics Recycling Council (HPRC), facilitated by Antea Group, is currently conducting a pilot in the Chicago area to address this waste and realize the financial and environmental opportunities. In the pilot, non-hazardous plastic is collected from hospital clinics, processed locally and prepared for reuse in other products. This kind of multi-stakeholder collaboration is a key recommendation in the New Plastics Economy report and a necessary ingredient for circular economy success.
Industrial sector pilot for reusing and recycling plastic scrap
The industrial sector represents a major opportunity for recycling plastics from post-manufacturing scrap. In spite of the opportunity, there are big challenges for plastics recyclers in being able to remain profitable. Recycled plastics have to compete with virgin plastics in quality and cost. The downward trending cost of manufacturing of virgin plastics puts huge pressure on the price for recycled plastics.
In order to be profitable, the plastics recycler has to deal with answering a multitude of questions: Which materials should be accepted based on quality or level of contamination? What is the cost to source materials? How efficiently can materials be transported to processing facilities? What level of processing should be invested in? And how should processed materials be priced for the market?
Cope Plastics, headquartered in Alton, Illinois, in conjunction with software firm Eco-Catalyst, based out of Silicon Valley, recently conducted a pilot study to improve the profitability of Cope Plastics’ already successful recycling operation. As market prices moved and capacity was strained, Cope needed to be able to identify not only load-specific profitability (pass-fail evaluation – a load was either profitable or not), but also margin. For example, Cope needs to quickly discern the difference in profitability between a load of plastic scrap from Omaha and one from Memphis, or a Gaylord from Little Rock versus a skid from Fargo. Plus, Cope’s executives wanted to have objective financial metrics as to the reuse-recycling operation’s profitability.
The Cope Plastics pilot leveraged Eco-Catalyst’s cloud-based software solution Smart EOL, and was anchored on three key strategies, outlined below.
1.) Cloud Based Data Management allows facility management to track and analyze direct and indirect costs, materials transportation costs and other essential transaction-related data in an easily accessible and inexpensive webbased system.
2.) Transaction Level Pricing enables the understanding of costs and profitability for each transaction so that the buyer or seller can make dynamic adjustments to the transaction based on market conditions.
3.) Operational Visibility through Analytics provides real-time visibility of volumes, revenues and prices based on inbound supplier shipments and outbound customer shipments, as well as trends on material mix percentages and visibility to prices of commodities associated with the materials involved in recycling.
Enabling a user interface that allowed for multiple users and real time data, Smart EOL allowed Cope Plastics to make better forecasts and choices at the agent level (rather than directing all decisions through management) thus enabling agents to make better real time decisions. Compiling the necessary data in one location also helped to maximize existing resources’ profitability. At the company level, this approach resulted in increased efficiency and a better understanding of environmental impacts and marketability, resulting in improved morale as well as new opportunities and partnerships.
Advice for profitable and responsible reuse/recycling of plastics
Both the Healthcare and Industrial pilots point to the imperative of identifying transactional value of post-use and scrap plastics, seeking out and understanding well-suited materials processing, and collaborating within and across industries to find regionally-close, costefficient and environmentally responsible reuse/recycling opportunities.
Most importantly – do not give up. Recycling plastics is the right direction for industries and the planet.
And the work continues. Antea Group is currently planning an HPRC-type consortium enabling the electronic-product chain, through pilots, to proactively support the circular economy, and Eco- Catalyst is conducting multiple pilots for materials recovery in Silicon Valley and in other regions and industries.
Dr. Ramesh Srinivasan is CEO, Eco- Catalyst, Inc.; Pamela J. Gordon is senior consultant, Antea Group; and Andy Fergurson is environmental manager, Cope Plastics. The authors wish to thank Jonathan Levy of ISRI for requesting and hosting the workshop ,“How to Make Money in Plastics Recycling,” presented April 6, 2016 at the ISRI Annual Convention. This article is based in part on that workshop.