Rubber-modified asphalt is an outstanding option for end-of-life tires
Let’s put more RMA in our roads; an interview with Granutech's Mike Hinsey
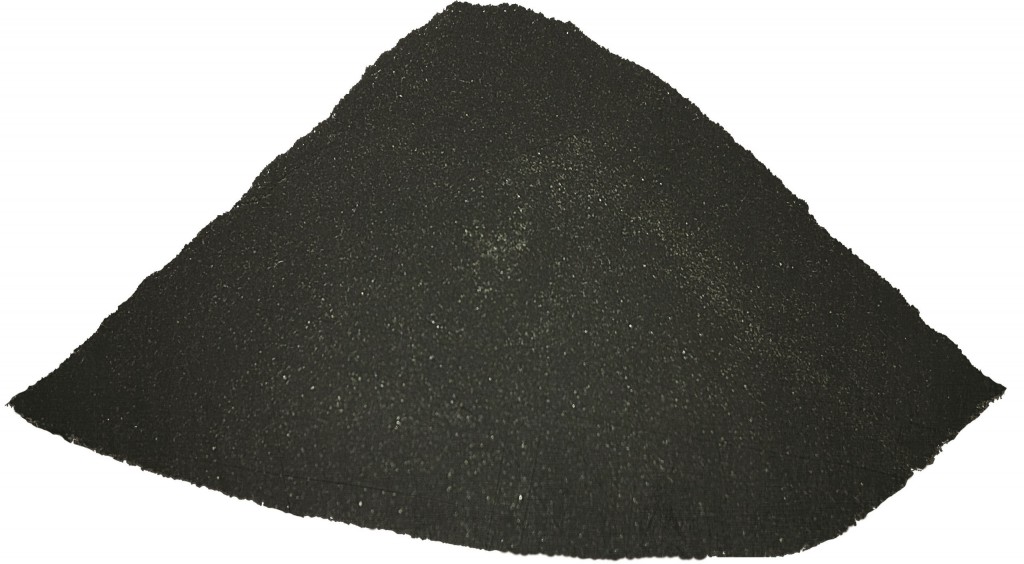
As recently as the 1980s, most scrap tires generated in North America were landfilled, stockpiled, burned or left lying wherever their last “roll” took them. Some market development and tire recycling was initiated in the 1980s, but tire dumping was still cheap and unregulated, so tires were not widely recognized as a resource until well into the 1990s.
According to a 2012 “Study of Potential Scrap Tire Markets in Canada” done on behalf of the Canadian Association of Tire Recycling Agencies (CATRA), during the 1990s “In addition to basic recycling objectives, a series of major stockpile fires encouraged provinces and states to initiate scrap tire management programs to stop illegal disposal and create markets.
“Many tire processing methods and equipment components were tried, with mixed results, and market development efforts tested the limits of creativity and ‘credibility’.”
According to the study, “The longterm result has been development of diverse products and a tire processing industry capable of making these products. In the relatively short period of 15 to 20 years, scrap tires have progressed from a disposal liability to a valuable resource with broad market penetration.”
Scrap tires definitely offer a range of possibilities for the manufacture of recycled products, from sports field and playground surfaces, to moulded products. Tire-derived fuel (TDF) is also a solid waste-to-energy option. And then there are our roads – millions of kilometres in North America which are nothing if not an end market with endless potential. This is where rubber-modified asphalt (RMA) comes in.
RMA technology was initially developed in the 1970s, has been actively promoted since the 1990s, and has continued to evolve. The technology is often referred to as the “Arizona Process” because of its extensive use within the State of Arizona. Variations have been developed in an effort to address perceived obstacles and improve performance. In each case, rubber is mixed with an asphalt binder, then the asphalt binder is mixed with the aggregate and spread on the roadway to form asphalt pavement. RMA is widely used in the U.S. (especially in the South) and increasingly across Canada.
Recycled tires – The not-so-long road to the highway
According to Mike Hinsey, International VP at Granutech, a manufacturer of shredders, granulators and mills for the recycling of end-of-life tires and rubber, recent reports from the Rubber Manufacturers Association tell us that in 2014 just over 200 million pounds of crumb rubber was utilized for RMA generated in the U.S. and Canada.
“RMA, sports field and playground surfaces, moulded products, and the landscape industry are the four biggest end markets for recycled rubber,” says Hinsey. “For the most part, the asphalt manufacturing industry needs a finer granulate than the crumb rubber generated and produced for sports fields and other end markets. It wouldn’t surprise me if 40 to 50 percent of U.S. producers who are making granulate (or powder) from end-of-life tires supply product to the asphalt manufacturing industry in some form or fashion.”
For the most part, RMA applications require 30-mesh (0.6 mm) or smaller granulate. To produce granulated recycled rubber suitable for RMA applications, end-of-life tires and rubber products are first shredded then put through a grizzly grinder to separate the steel, and then through a granulator to get a near fibre-free product. The final stage – the one that gets the crumb rubber to the size needed for RMA applications – is the mill.
“We’ve recently introduced our updated G-4X mill, with a true roller-bearing design rather than a bushing,” says Hinsey. “This allows the machine to hold much tighter clearances, reduces bearing temperature, reduces grease consumption and increases production out of the mill. So we can take the same mill, now fitted with bearings instead of bushings, and increase a rubber recycler’s production while reducing his operating costs and wear and tear on machinery.
“On the production side, there are challenges with respect to making a relatively clean material – one that doesn’t have a lot of contamination. At Granutech, with the systems we supply for producing granulized rubber, including the new G-4X Mill, we added in de-stoning processes to capture non-ferrous contaminants like brass, lead, aluminum, stones and glass. It is an added separation process, which follows the mill.”
Hinsey continues, “What makes this technology unique for the asphalt industry is that recyclers can now use technology such as our G-4X mill to efficiently and consistently make the fine-grind powder (minus 30 mesh material), to specifications needed and at a high capacity.
“Those that tend to make asphalt quality material generally do so with a G-4X-style twin drive mill. Key features of that style of machine are the ability to get a high friction ratio and a much greater number of cuts per revolution, which is very, very important for producing asphalt rubber.” Hinsey says that if there is one drawback to the use of RMA, it is that it is generally a product that has to be put down during a warmer part of the year. Thus, northern climates are more restrictive, with respect to the “window” available for the application of RMA.
In the State of California, they recently put legislation in place mandating the use of RMA on an incrementally rising scale, approaching a 50 percent requirement for RMA in state asphalt projects.
“Arizona probably leads the U.S. in terms of the percentage of road paving projects that require rubberized asphalt,” continues Hinsey. “You go all across the southern U.S. at this point, from Texas to Florida – they are all using a large amount of RMA in their road building. The northern states and Canadian provinces as well, but they’re limited by a shorter season.
“If rubber-modified asphalt was used across all of the main highways in North America where we use asphalt, we could resolve the scrap tire challenges we have in Canada and the U.S. There has been some progress over the last decade in using more RMA in our roads, but there are still many who want to build roads the same way it’s been done for decades, even if RMA roads have shown that it’s a better performing product and has a lower life cycle cost.
“The benefits are proven,” concludes Hinsey. “Reduced noise is definitely a major benefit of RMA-built roads in urban areas and, more importantly, wherever RMA is being used, they’re seeing a substantially longer overall life of their asphalt pavement, compared to traditional asphalt. “When it’s put down properly, at the right time of year, with the right conditions and right temperature, rubber modified asphalt performs superbly, regardless of the climate.” RPN