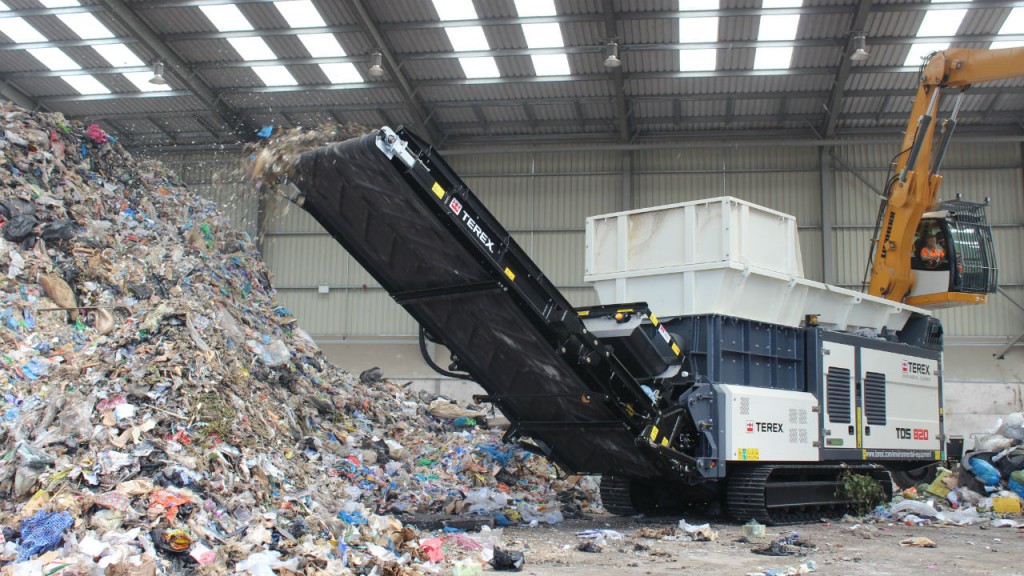
Terex Environmental Equipment (TEE) houses an impressive and diverse lineup of grinding and shredding products that is capable of processing a number of applications for both North American and European end users. As mentioned in the March issue of Recycling Product News, TEE’s infusion of horizontal grinders from Continental Biomass Industries (CBI) has given the large equipment manufacturer the horsepower to compete across the globe in a variety of grinding applications. As for its slow speed and medium speed shredding machinery, TEE has continued to meet the challenge of customer production needs as well.
Several months ago at the 24th Annual Compost Show, TEE and its expansive Ecotec product line showcased its versatility as attendees watched nearly a dozen of its products in live operation. Among the machines available for viewing were those belonging to the CBI Legacy Grinders -- the TBG680 (CBI 6800BT) and TBG650 (CBI 5800BT). With ease, the machines processed palm trees and land clearing debris. Meanwhile, the TDSV20 Medium Speed Shredder also processed the same material while the TDS820 Slow Speed Shredder processed construction and demolition waste (C&D).
The advantages of application diversity, ease of machine transportation and automated material protection systems has many across the wood processing, biomass production and recycling equipment fields believing that TEE machinery is growing stronger than it has already.
“With the acquisition of CBI, TEE’s Ecotec line has quickly taken shape as we continue to develop and spread the word of our products to dealers and customers across the United States and Canada,” said TEE Ecotec North American Sales Director Art Murphy. “The response from our expanding dealer network has been outstanding as we continue to show them how deep our product line is and the benefits of partnering with Ecotec.”
Murphy can directly attest to the positive reputation of the CBI Legacy Series, which includes both the TBG680 and TBG650 high speed grinders (among others). Designed for processing waste wood, either as a primary or secondary grind application, both machines feature a hog box with a clamshell opening for ease of maintenance. Here, machine operators can change out screens and tips without confined space being an issue. Also, each CBI Legacy Series grinder comes equipped with the patented Metal Detection System (MDS).
“The MDS helps protect the machine from tramp metal, steel and contamination,” said CBI Controls Engineer II Adam Knight. “Without it, you’re relying on the operator to stop the machine and shut it down to get the metal out. A key component of the MDS is it pulls the engine RPM down as soon as tramp metal is detected. The diesel engine by nature wants to try to increase power to overcome the foreign object. This only creates more damage. The MDS tells the engine to idle down immediately, so it’s not trying to power through the foreign material that is in there.”
The MDS is designed to protect the rotor, anvil and screen. It senses metal impact, reverses the feed system, liftsthe top feed roll, reduces engine speed, disengages the clutch and shuts down the engine. This series of steps occurs just milliseconds after tramp metal is detected by impact sensors.
“The TBG650 is a monster of a machine and simply unbelievable,” said Jason Smith of Boseman Farms and Eastern Compost, LLC in Brattleboro, North Carolina. “We’ve had about six different grinders before this one, but this is our first tracked unit and its MDS was a major selling point for us.” The TBG 650 was purchased by Boseman Farms late last summer from Powerscreen Mid-Atlantic, Inc.
“We grind a lot of pallets and crates that are full of more than just nails and screws,” he said. “Occasionally, metal objects such as crankshafts or flywheels are still located in the crate during the grinding process. This is where the MDS comes in to prevent anything from going through the grinding chamber that shouldn’t. It really helps us out knowing the foreign materials are being kept away.”
Like the grinders, TEE shredders are also equipped with protective programming should any foreign objects enter their double shaft shredding chamber. The TDS820 includes a hydrostatic drive that provides increased protection against contamination as its independent gearboxes enables both 79”shafts to run separately. Each shaft is manufactured with a fully-welded tooth configuration, which makes for massive throughput and excellent material reduction.
Both shredders also share a user-friendly control interface, complete with pre-installed programs that are customizable to allow operators to tailor the machine for specific applications. Both shredders can process household waste, bulky waste, commercial waste, waste wood, tires, green waste and forestry waste. The TDSV20 is the first when it comes to the mobile shredder sector. The machine, which operates up to 160 RPM and is equipped with precise machined bolt-on cutting teeth, highlights TEE’s ability to design and manufacture products that are demanded by modern day customers.
Depending upon the engine type, the shredders and grinders satisfy Tier 4 Final standards to meet the latest regulations in emission reductions of particulate matter and nitrogen oxides. The TBG680 is powered by a CAT C-27, 1,050 HP diesel engine (available as Tier 4 Final) and the TBG650 is powered by a Caterpillar C-18, 765 HP diesel engine (also available as Tier 4 Final). The two shredders also have a flexible engine package to suit whichever geographical emission regulations an end user needs to follow.