Building the world's most advanced MRFs
BHS begins installation of world’s largest multi-material processing system and opens $33 million facility in UK
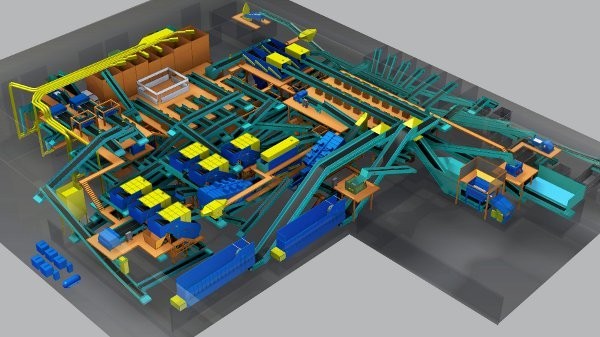
Installation has begun on what is considered to be the largest and most extensive multi-material processing system in the world. The facility, at the Newby Island Material Recovery Facility (MRF) and Composting Operation in Milpitas, California, is owned by Republic Services, Inc. Republic Services says they chose Bulk Handling Systems (BHS) to design, manufacture and install the custom-designed, highly-automated system. Installation of the 110 tons-per-hour system began earlier in 2012 at the facility, with operations slated to start later this year.
The system will process commercial material from the City of San Jose, recovering all recyclables and utilizing organic material as feedstock for further waste-to-energy processing, allowing the city to meet its progressive diversion goals. In addition, the system includes capacity for up to 120,000 tons per year of residential single-stream material.
BHS says the highly-automated system incorporates the world’s most advanced screening, optical, and air separation technologies and is designed to maximize the recovery of marketable commodities and dramatically reduce the material going to landfill in San Jose. The recovery rate is expected to exceed 75 percent on the commercial lines and 95 percent on the residential single-stream line.
The expansive system consists of four processing lines: a residential single-stream line, a commercial single-stream line, a commercial dry recyclables line and a commercial wet recyclables line. The system also features a glass clean up system and a shared container line with seven optical sorting units.
“Republic is pleased to be working with BHS on this extraordinary project,” says Mark Buntjer, Northern California Recovery and Recycling General Manager at Republic. “This facility is the first and largest of its kind and we’re excited to be at the forefront of the industry, setting the pace globally for multi-material recovery.”
“All of us at BHS are extremely honoured to be working with the team at Republic Services on this unique and unprecedented facility,” says Steve Miller, BHS CEO. “It truly is the first of its kind and is a fantastic example of how the scope of our industry is expanding to recover materials from a wide variety of waste streams.”
$33 million MRF opened at Casepak, UK
Casepak, a leading UK waste management company celebrated the official launch of its $33 million Materials Recovery Facility in Leicester, England, on January 16, with presentations and tours of the facility which features a custom-designed sorting system engineered, manufactured and installed by BHS. Environment Minister Lord Taylor of Holbeach attended the event as guest of honour. “There are huge business opportunities in the growing recycling industry and Casepak’s investment in this new plant is already showing rewards,” he said.
“This is a major milestone for Casepak,” said Mark Smith, managing director at Casepak, “Since the MRF became operational in September we have already secured contracts to manage several local councils’ recyclable material streams and we aim to do more of the same in 2012.”
Due to the highly efficient and effective BHS design, Casepak says they are able to process material at rates significantly beyond the design capacity of 26 metric tons per hour. Production was also recently boosted with the addition of a second shift. As soon as its first week of operation, the system was exceeding design capacity, while delivering high recovery rates of more than 95 percent of the available commodities, at extremely high purity levels.
“Our new MRF has been developed to meet the demands of changing collection systems at the same time ensuring we produce a quality end product,” says Kevin Thomas, Casepak’s director, MRF operations. “This is not a waste treatment facility – it’s a production process for essential materials and, as with any production process, quality is the key. Our system is based on a combination of robust screen and optical sorting technology to achieve the best possible quality output.”
According to Casepak officials, the new facility is the first in the UK to incorporate screening technology to recognize and separate the highly compacted plastic and metal food packaging found in household recycling collections.
“We are the first MRF to import this technology from the USA,” says Thomas. “It ensures that items such as small plastic bottles and yogurt cups that are easily squashed during the collection process are identified and separated, ensuring that they are recovered and retain their resource value.”
The MRF in Leicester also features a patented BHS De-Inking Screen which separates fibre grades – another key factor in the purity of commodities, Thomas says. In addition, the system includes a mixed fibre optical unit, film handling system and full optical container line for plastics recovery.