The time is here to get on board the scrap export wagon
New horizontal loading technology helps get the job done quickly, safely and without container damage
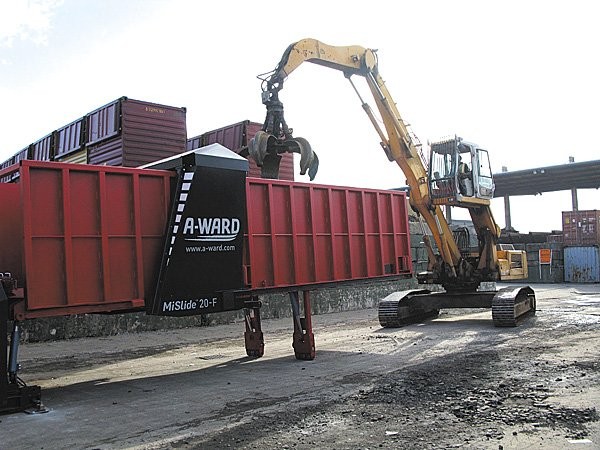
When it comes to exporting scrap metals, or any other product for that matter, efficiency is paramount. You must be smart, play smart and employ smart tools if you want to compete in a rapidly expanding market.
Due to continually improving global freight systems, which have driven down export scrap costs, global scrap prices are becoming more common. This means companies need to differentiate themselves to stay ahead of the pack.
In the past ten years, and particularly since 2005 there has been a phenomenal increase in scrap steel exports, and this is a trend that is expected to continue for some time. In North America alone, scrap metal steel rates more than doubled in a six year period – from 18 million tons in 2005, to over 36 million tons in 2011.
This trend has coincided with companies looking for better ways to do business – paying more attention to foreign markets, and shifting business focus to setting up operations for export.
In 2006, A-Ward launched it’s now popular Container Tilter. Since then, over 100 of these machines have been installed in yards across North America, and over the last several years, the company has been working closely with its customers to develop the next “revolutionary” new container.
Introducing the MiSlide
At the 2011 Institute of Scrap Recycling Industries Convention in Los Angeles, the MiSlide 2040 horizontal container loader was launched in North America. According to A-Ward the product received fantastic reviews at the show, and its smart and simple design means that it can be priced to suit any size recycling company.
MiSlide is a horizontal container loader designed to load 20- and 40-foot containers with both light and extremely heavy gauge material. The result, according to A-Ward, is faster, safer, economical and more user- friendly container loading, and zero container damage. Named after its unique sliding system, the MiSlide allows a container to arrive empty and then leave a yard full in as little as five minutes.
“Every part of business operation’s must work smarter to survive,” says Simon Ward, A-Ward’s managing director. “Ask yourself why some companies fail and other succeed in the same market.”
Ward says a common complaint of those companies already using horizontal loading methods was the time it took to perfectly line up the truck and trailer unit and then also connect the shipping container to the machine. A-Ward’s answer is a simple hydraulic alignment control.
As the truck is reversing towards the MiSlide, the machine operator is able to adjust the unit up and down, and from side to side, from the safety of a cab. This ensures that the reversing trailer is perfectly aligned first time, every time – eliminating corrections of the entire vehicle and costly waiting.
Another time-saving feature of the MiSlide is a unique automatic container locking and unlocking mechanism called the ‘Auto-Locker.’ This innovation removes the need for an employee to manually lock the machine in place. Overall, A-Ward says the MiSlide’s ultra-fast loading times can slash transport and wage costs, and create huge efficiencies within an operation.
“A truck shouldn’t wait to be loaded ever, as this time costs money,” continued Ward. “The MiSlide pre-loads material before the truck bin or shipping container arrives, with the perfect weight and distribution. Trucks are in and gone again in minutes.”
A smarter way to load
According to A-Ward, in order to craft the “safest loading system in the world” they had to eliminate the need for manual interference. MiSlide has two state-of-the-art features that keep operators in their cabs and therefore eliminates safety risk. These, as mentioned, are the remote controlled hydraulic alignment and the Auto-Locker.
The Auto-Locker is a smart, highly durable device which automatically connects to the shipping container when the truck is reversing. It then automatically disconnects from the shipping container when the container is full and the truck is ready to drive away – meaning no human hands are required.
Achieving accurate weight is also vital in container loading. With the MiSlide, A-ward says users will avoid the costly mistake of inaccurate weight, which results in containers having to be re-opened and loads adjusted. The accurate weight systems incorporated into both the MiSlide and A-Ward’s container tilters ensure that maximum weight loading can be achieved every time. Moreover, the real-time weight is displayed on the remote control screen inside, ensuring that the machine operator does not have to leave the safety of the cab.
“The benefit of the MiSlide that we are most excited about is the fact that there is no high maintenance telescopic ram,” says Ward. “The collective feedback from companies who have purchased other horizontal loaders was that the operating and servicing costs and complexities associated with a huge telescopic ram were a lot higher than expected. Not to mention the daunting realization that their expensive telescopic rams would likely need to be replaced in the future.”
Plus, by eliminating the need for a telescopic ram, the MiSlide runs on a 23-hp motor. According to A-Ward, the fuel costs of operating the MiSlide, for a busy day of loading, are a fraction of the costs associated with other horizontal loading techniques. The design of the MiSlide also ensures that service and maintenance is almost non-existent, and wage costs can be slashed by making the container loading process a one-man operation.
Ward says the other goal during development of the MiSlide was to create a loading machine that causes virtually no container damage, especially when loading extremely dense materials. The solution is a system where the shipping container encapsulates the loading machine and drives forward, holding the load inside. This, opposed to a loading machine pushing the material in, which can cause all sorts of scraping and bulging issues.
The choice between a horizontal loader and container tilter depends on the type of material being loaded and the size of the shipping containers being used. For example, when loading shredded steel and HMS (heavy melting steel) into 20-foot-only containers, filling at 90 degrees with a container tilter enables maximum weights to be achieved.
In A-Ward’s experience, many companies who were previously forced to load HMS into 40-foot containers to achieve maximum weights are now able to shrink shipping costs by more efficiently loading 20-foot containers tilted upwards. For yards loading light gauge as well as very heavy gauge material, requiring both 20-foot and 40-foot containers, MiSlide is an ideal solution.
A-Ward says their technology is also an excellent option for loading extremely dense materials which simply cannot be dropped from a height. In many situations where quantities justify it, the most efficient set-up may include having both a container tilter and horizontal loader.
So, what does the future of global scrap steel market look like? Trends over the past few decades show that scrap steel exports are increasing at an exponential rate and this is likely to continue for some time. What does this mean for those in the scrap industry?
“If you aren’t already on the scrap steel export wagon, we would recommend you jump aboard,” says Ward. “If you are already on board, now’s the time to start playing smart. Get the tools to give your operation the competitive advantage in this rapidly expanding market, and load more profit into your back pocket.”