How wood waste grinder screens make a big difference for quality end product
Wood waste processors have many considerations to keep in mind when selecting horizontal wood grinder screens
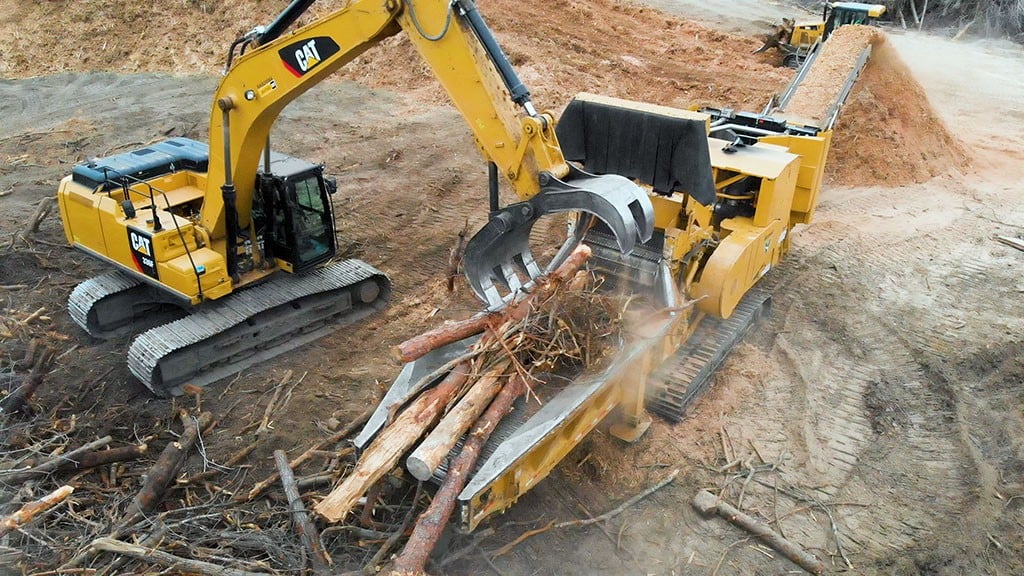
Wood waste processors face a variety of considerations when selecting the screen configuration to best accomplish a desired end product from their wood recycling equipment. Screen selection and grinding strategy will vary based on a variety of factors including the type of grinder being used - horizontal versus vertical - as well as the type of wood waste being processed, and will also differ based on tree species.
Why use round screens for tub grinders and square for horizontal?
"I usually tell customers round screens for round grinders (tub) and square screens for square grinders (horizontal), but there's an exception to every rule," says Jerry Roorda, an environmental application specialist for wood recycling equipment manufacturer Vermeer Corporation. "Using a screen with round holes in a tub grinder will result in a more consistent end product compared to a square-hole screen due to the geometry of the hole."
Screen selection can change depending on two major factors - the type of material being processed and the end product specifications.
Tree species react differently to grinding
"Each tree species is unique and will produce a different end product," says Roorda. "Various tree species will react differently to grinding often because the grain of raw wood can make a widely varying product that can have a big impact on the type of screen used."
Even the moisture content of the raw wood waste material has an effect on the end product and the type of screen to be used. You may grind waste wood from the same location in the spring and then again in the fall, but the final product may be different due to the moisture content and the amount of sap in the waste wood.
What shapes and sizes of screens for wood waste grinders are available?
Round and square
The most commonly used screens in horizontal wood grinders feature round and square holes as these two geometric configurations tend to produce a more uniform wood chip particle size and end-product across a wide range of raw materials. There are other options, however, and each serves a specific function depending on the application.
Diamond hole
This is ideal for processing wet and difficult-to-grind waste material such as compost, palm, wet grass and leaves. The particle size of these materials have the potential to build up on the horizontal plane of square-hole waste wood shredder screens or between the holes of round-hole screens, causing the screen to blind and the wood waste material to re-circulate, thus reducing overall productivity.
A diamond-hole screen is designed to channel the material to the point of the diamond, which allows the cutter to swipe past the screen, helping to remove the types of material that may otherwise accumulate.
Grid
Bars are welded horizontally across the screen face (as opposed to a rolled punch-plate screen) and function similar to a secondary anvil. A grid screen is often used in applications such as processing of industrial wood waste such as construction debris or in land clearing applications where there is less concern about the specification of the end product but more is needed than standard wood chippers.
Rectangular
This allows more wood scrap material to pass through the screen due to the increased geometric size of a rectangular-hole opening compared to a square-hole opening configuration. One potential drawback, however, is that the overall consistency of the end product may be compromised.
Hex
Hex screens provide a more geometrically consistent hole and uniform opening, as the distance between the corners (diagonally) is greater on a square hole than in a hex hole which is straight. In most cases more material can be processed with a hex screen — versus a round-hole configuration — and similar wood chip production values can still be achieved, compared with a square-hole screen. It is important to note, however, that actual production rates will always vary based on the type of material being processed.
What are the cutting dynamics of a tub wood waste grinder compared to a horizontal grinder?
The cutting dynamics of a tub and horizontal grinder differ dramatically. As a result, horizontal wood grinders may require the use of special screen setup configurations in some applications to attain a specific desired end product.
When using horizontal wood grinders Roorda suggests using a square-hole screen with the addition of baffles to help reduce the likelihood of producing oversized wood chips as its final product.
The baffle is a piece of steel that is welded on the back side of the screen - a design configuration that will help prevent long shards of scrap wood from passing through the hole before it is properly sized.
Compare baffle size to hole size
According to Roorda, a good rule of thumb for adding baffles is that the length of the steel extension should be half the diameter of the hole. In other words, if a 10.2cm (four-inch) screen is being used, the steel baffle should be 5.1 cm (two inches) long.
Roorda also points out that although step screens can be used with tub grinders, they are often better suited for horizontal grinders, since the configuration of a step screen helps reduce recirculation of the ground material which often has a tendency to produce nugget-type wood chips as an end product.
Should you do a one pass grind or two passes?
There are varying opinions on whether production using a one pass grind through a wood grinder is more cost effective than a pre- and regrind process. Again, efficiencies will likely be determined by the type of material being processed and desired end product specifications. When processing a whole tree, for example, achieving a consistent end product will be difficult with a one pass approach given that the raw scrap wood material being ground is not uniform.
Roorda recommends making an initial trial run using both a one- and two-pass process to collect data and compare rates of fuel consumption relative to the volume of end product produced. Most processors may find it surprising that, in most cases, the two-pass, pre- and regrind method may be the most economical production method.
What proactive screen maintenance should be done on wood waste grinders?
Manufacturers recommend that grinder engines used in the wood processing industry be serviced every 200 to 250 hours, during which screens and anvils should also be inspected for wear.
Maintaining consistent spacing between the cutter and anvil is critical to producing a quality, consistent end product through a wood grinder. Over time increased wear to the anvil will result in increasing the space between the anvil and cutter, resulting in the potential for wood chips to pass through unprocessed. This may impact cost of operation, so it's important to maintain the grinder wear surfaces. Vermeer recommends that anvils be replaced or repaired when obvious signs of wear are apparent, and that hammers and teeth are inspected daily for wear.
Inspect between cutter and screen regularly
The space between the cutter and screen is another area that should also be inspected on a regular basis during production. The gap is likely to increase over time due to wear, and so productivity may be affected. As the distance increases it will result in recirculation of processed material, which can also affect the quality of end product wood chips, productivity and increased fuel consumption.
"I encourage processors to track their cost of operation and monitor productivity levels," Roorda says. "And when they begin to realize a change, it is often a good indicator that the parts most likely to wear should be inspected and replaced.
How are wood waste screens different?
At first glance, one wood grinder screen may look similar to another. But a more in-depth inspection will likely reveal data showing this is not always the case. Screen manufacturers - both OEM and aftermarket - may use different types of steel, and what may appear to be a good deal on the surface may actually end up costing more down the road.
"Vermeer recommends that industrial wood recycling processors select a screen constructed with AR400 grade steel," Roorda says. "AR400 grade steel offers enhanced wear characteristics compared to T-1 grade steel, a raw material often used by some aftermarket screen manufacturers. The difference isn't noticeable on inspection so processors should make sure they always ask the question."