New filtration system for highly contaminated plastics boosts recycling productivity and minimizes melt loss
Automatic self-cleaning system from Nordson maintains constant melt pressure and uses filter element with long working life
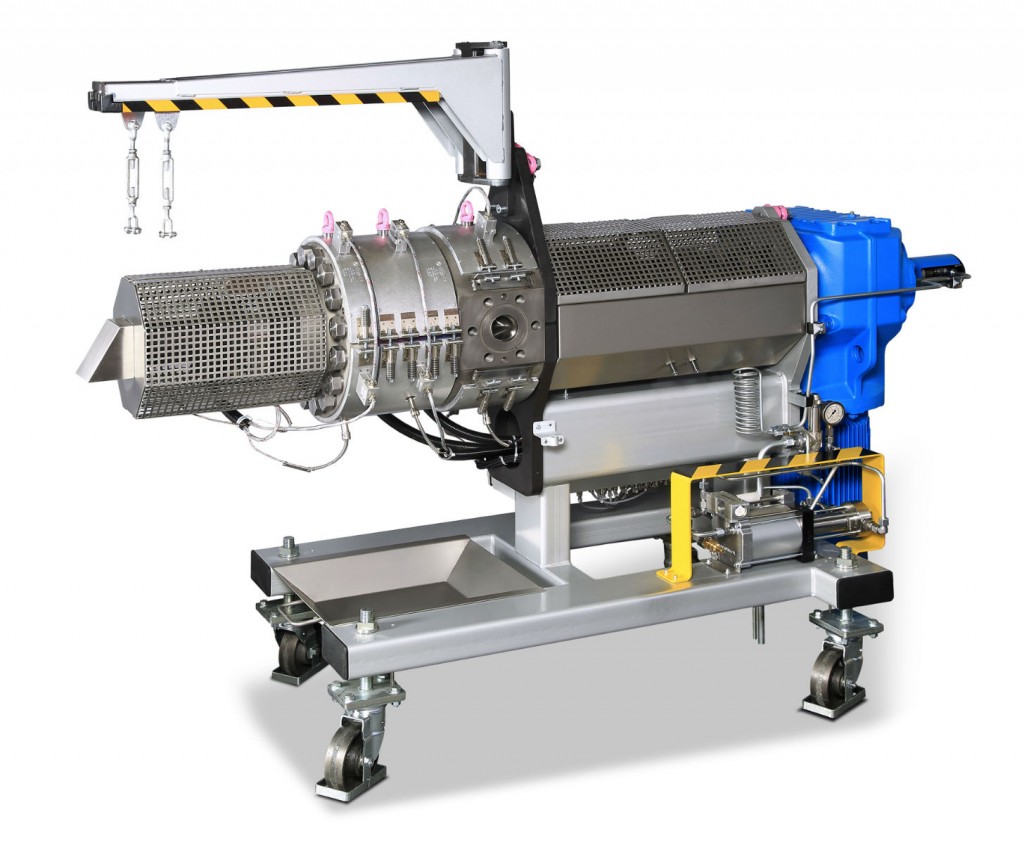
A new melt filtration system designed for recycling highly contaminated plastics provides greater productivity than comparable machines on the market while maintaining constant melt pressure and product consistency, according to Nordson Corporation, which introduced the system this month, globally. Tradenamed BKG HiCon R-Type 250, the Nordson Polymer Processing Systems (PPS) equipment transforms highly contaminated polyolefin or styrenic plastics into clean, high-quality material and exhibits less melt loss than with traditional backflush systems for highly contaminated plastics, according to Nordson PPS business unit director, Sven Conrad.
Conrad says the central concept of the HiCon R-Type 250 system is unique. It involves the use of a cylindrical “separating head” with knives arranged on its surface in a helical pattern designed to move contaminant particles forward as the head rotates. Enclosing the head is a stationary filter element called a “strainer tube.” When contaminated melt from an entry port flows into the cylindrical space between the rotating head and the strainer tube, the knives capture the contaminant while the contaminant-free melt moves through the strainer into flow channels that lead to an exit port. At the same time, the rotating head turns a screw which guides the contaminated material through cooling sections and finally to where it is discharged into collecting bins.
“Nordson’s newest development cleans much more efficiently than commercial available filtration systems for highly contaminated polymers,” said Mr. Conrad. “The special design makes possible a uniform load on the strainer tube during the cleaning process, providing an extended lifetime for the filter and scrapers and increasing the overall efficiency of the system at far less melt loss.”
A powerful drive actuates the separation head / discharge-screw assembly. The HiCon R-Type 250 system operates at a maximum pressure of 350 bar and maximum temperature of 320 °C. Throughput can range from 500 to 1,500 kg/h. The rate depends on polymer viscosity, filtration fineness, levels of contamination, and other factors. As it exits the system, filtered polymer is maintained at a constant pressure, ensuring uniform processing downstream.
One key to the efficiency with which the HiCon R-type 250 system removes contaminants is the design of the steel strainer tubes, which are available with micro-holes ranging from 120 to 750 microns. The holes are conical in shape, permitting passage of molten polymer while preventing blockage by contaminant. This design and the symmetrically positioned knives in the drum contribute to the long working life of the tube before it needs to be replaced. Once cleaned, moreover, the tube can be reused.
Replacing a strainer tube is facilitated by a built-in swiveling arm for removing the strainer tube housing, and by a hand-operated hydraulic device for disassembling it. To ensure uninterrupted production, it is possible to operate two HiCon R-type 250 systems in parallel.
“A network of several Siemens SIMATIC control and monitoring units contributes to the high level of automation and ease of use that distinguish the HiCon R-type 250 system,” said Rolf Schultheis, Nordson PPS manager of electrical engineering. “The Siemens control system is intuitive, instantly providing a visualization of all process parameters. The onboard Ethernet / Profibus interface opens the possibility of integrating communication with other devices, collecting and recording production data, and even performing remote maintenance.”
HiCon R-type melt filtration systems are available from Nordson worldwide. The company offers localized sales and technical support services in countries around the world. Other Nordson brands of interest to recyclers include Nordson PPS melt pumps, Xaloy extruder screws and barrels, and BKG pelletizers.