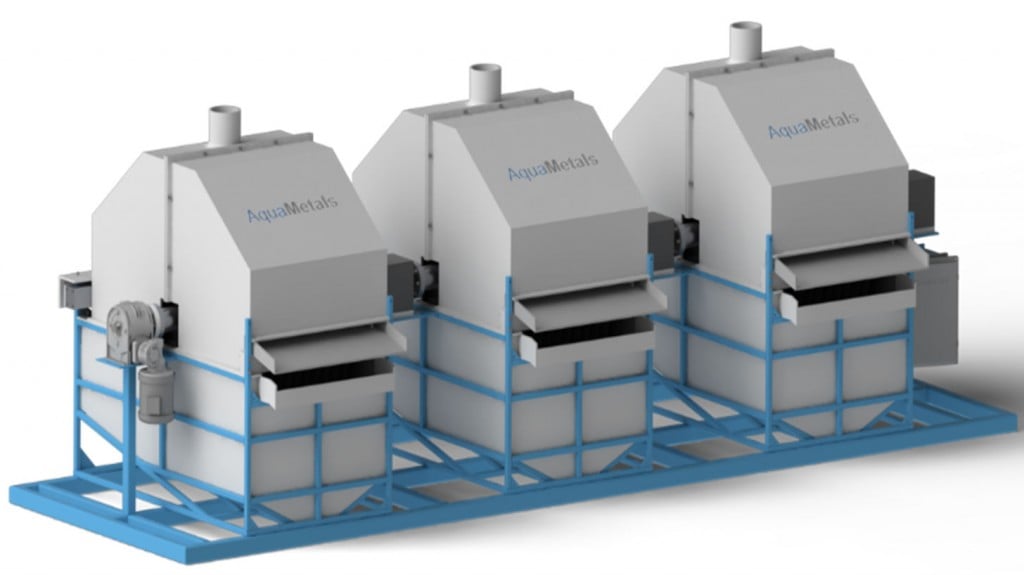
Over 95 percent of the World’s rechargeable batteries use lead-acid chemistry to store and release energy. Lead-acid batteries (LABs) are ubiquitous for automotive, power sports, energy storage and backup power supplies for hospitals and data centers. Demand for LABs and lead to make them with has almost doubled in the last decade.
What to do with spent batteries, of every kind, has long been a major environmental challenge. Many newer battery chemistries, such as lithium ion, are fundamentally unsuited to commercial recycling and do not have an established collection infrastructure. Consequently, ensuring that their toxic contents remain out of the environment at their end of life is a major challenge.
In this regard, LABs are unique as they are >99% recycled and in the US more than 70% of the lead in new LABs is recycled. This exceptional recycling rate is driven by simple economics - money can be made doing it. Consequently, in most of the developed World, LAB collection and recycling supply chains are an integral part of the production and distribution cycle. This delivers multiple benefits, including eliminating land-fill at end of life and significantly reducing the need to mine and process new raw materials.
However, it’s not all good news, the current LAB recycling technology – lead smelting – has arguably reached the end of its development life and struggles to meet ever tighter emissions standards. In the developed world, expensive and problematic filtering technologies are required to limit and manage emissions of lead dust and other toxic materials. In developing nations, these are often missing and unregulated smelters have become a major environmental problem. Unacceptable levels of lead exposure to local populations, long ignored in the West, are now starting to impact the Western LAB industry as its customers increasingly require proof of source for the lead in its products.
Lead smelting operates at more than 1400F and is an energy intensive process. Large amounts of fossil fuel are needed with significant CO2 and other green-house gas emissions. Chemical processing agents such as limestone, fluxes, coke, soda ash and even arsenic are required to separate the oxides and other impurities from the recovered lead. This results in the generation of significant lead and other heavy metal contaminated solid waste.
In the U.S. three large smelters have closed due to environmental violations, leaving fewer compliant facilities spaced farther apart. As such, transport costs are starting to become a challenge to efficient LAB collection and recycling.
It is clear there is a problem with our current LAB recycling process and as the world now uses approximately 11 million tons of lead annually (according to CHR Metals), a cleaner and more cost efficient recovery and recycling method is needed.
One new approach is a closed-loop, electrochemical process that we call AquaRefining. Inspired by other waste management technologies, this process can be broken down into three main parts:
1. Breaking and separation: Spent LABs are processed through a modern battery breaking process, which separates the plastic, sulfuric acid and other components from the lead. This is a liquid-based process from which water and plastics are recovered for reuse and sulfuric acid is recovered or neutralized.
2. Digestion: Lead is dissolved through a proprietary, non-hazardous, biodegradable and water-based electrolyte in a safe, room-temperature process. The electrolyte solution is also pumped through a closed-loop process and is recycled repeatedly, rather than being expended in one cycle.
3. Electrolysis: Lead dissolved in the electrolyte solution is then recovered by a completely new and proprietary continuous electrochemical process. Importantly, the resulting lead is purer than can be produced by smelting alone.
AquaRefining is an automated, room-temperature, closed-loop process that uses liquids and electricity to replace fire and powders. It emits no slag, no toxic waste and almost no off-gas. Importantly, it is a wet process which reduces or even eliminates lead dust and fugitive emissions. AquaRefineries are capable of processing the same volumes of lead that smelting can. However, AquaRefining can be implemented flexibly, cost effectively and in smaller facilities which are able to meet even the strictest of environmental regulations. This allows recycling operations to co-locate with LAB collection points and manufacturers. This has the potential to greatly streamline the supply chain and improve process economics, while producing high quality lead.
Changing the way LABs are recycled has the potential to revolutionize and revitalize an industry that is already far ahead of all other battery technologies in recycling rates. Solving the emissions, permitting and logistics challenges associated with smelting creates a unique and powerful opportunity for LAB manufacturers, distributers and recyclers to work together to promote the use of the only closed-loop and environmentally-responsible battery technology.