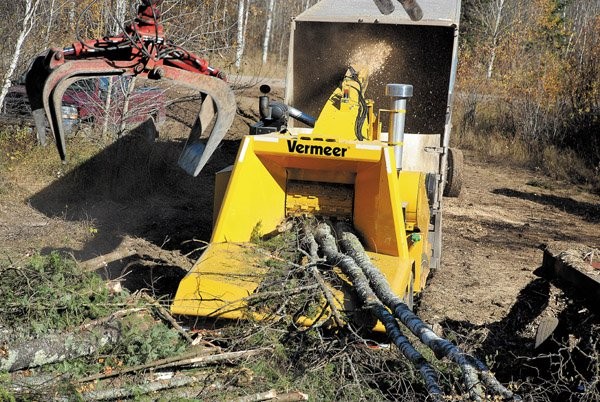
Vermeer Corporation has introduced the WC2300 whole-tree chipper, designed specifically to produce chips for the growing biomass industry, and with many proven technologies developed by the company.
“We spent considerable time working with end users to identify what features they thought were missing on current machines in the marketplace and incorporated those improvements into the WC2300 whole tree chipper,” said Mark Rieckhoff, environmental sales manager for Vermeer.
The heart of the WC2300 is its innovative infeed system that includes variable-speed; dual-infeed conveyor chains, a conveyor head pulley with integral grip bars and an aggressive large-diameter infeed roller with crush capability. These design elements provide efficient feeding of difficult material types, reducing the number of times an operator has to handle the material. In addition, the infeed conveyor chains are individually tensioned to accommodate unequal chain wear, allowing the operator to replace a single chain at a time.
Vermeer says customers will appreciate the replaceable wear components. The drum design, discharge chute, cutter housing and infeed conveyor floor are designed with bolt-in replaceable wear parts. This helps to extend machine life, and reduce down-time.
The WC2300 also offers two drum knife options — double-edged or babbitted single-edge cutter knives. These two options allow the operator to select the type of knife that best suits their operation, jobsite or customer requirements. In addition, the drum and cutter knife design provides two different knife-mounting depths of cuts, resulting in different chip sizes, allowing one machine to provide different end products to meet the needs of multiple end users.
Vermeer says the new WC2300's compact design allows for more maneuverability and easier repositioning of the machine on the jobsite. The tongue of these chippers is equipped with a grapple grip collar area allowing a log skidder to pick up the tongue and move the machine to a new location on the jobsite. The brake system includes extra air tank capacity and a brake release valve to allow the parking brakes to be released without hookup to a standard tow vehicle.
Machine functions can be controlled remotely using a handheld remote control. The remote allows the user to operate the WC2300 from another location — such as the cab the loading machine — and provides real-time machine performance data to aid the operator in maximizing productivity by monitoring and adjusting settings. Plus, down pressure of the infeed roller is monitored using the Vermeer exclusive SmartCrush system. Infeed roller down pressure is minimized until the feed roller has climbed up onto the material, and then automatically increases down pressure to feed difficult material with forks or large limbs to the cutter drum. Four different down pressure settings are available on the remote to match most material types. With material securely gripped by the infeed system, the operator can release the loader grapple and concentrate on the next load of material.
The infeed table on these machines features a 6-degree slope that lowers the "break-over" point where long material first contacts the machine. This provides for a smooth flow of long material from the ground up onto the infeed table and reduces the likelihood of limbs or tree canopy from snagging on the end of the machine.
A patented feed-sensing control system — SmartFeed — monitors engine rpm and automatically stops and temporarily reverses the feed roller and infeed conveyor when feeding larger, hardwood material. SmartFeed also senses feed roller jams and responds by automatically shifting material back and forth. This also helps increase operator productivity and reduces strain on vital engine parts. With four selectable rpm settings, the system offers improved versatility for varying applications and by controlling material jams; the need for grapple loader manipulation is reduced.
The WC2300 is also equipped with a 440-hp (328.1 kW) C-13 CAT diesel engine that allows for maximum output while consuming less fuel than higher-powered machines. The operator can engage the EcoIdle Engine Control System, which automatically lowers engine speed to 1400 rpm if no material has been chipped for 30 seconds, helping to consume less fuel if the feeding process has frequent interruptions. Engine speed automatically increases if the feed roller climbs up onto new material or the engine detects a change in loading.
Additionally, directing chips into a trailer has been simplified with a double-pivot chute that allows for hydraulic adjustment either vertically or horizontally to achieve the right angle for optimum trailer loading. Users can adjust the side-to-side sweep — up to 14 degrees left and right — and raise the chute up to 22 degrees or lower down to 14 degrees.